Production has begun at Dallas-based semiconductor giant Texas Instruments’ newest 300-millimeter wafer fabrication plant in Richardson. Company officials believe it will have a major impact on boosting wafer production for years to come.
Called RFAB2, the plant is connected to RFAB1, which opened in 2009 as the world’s first 300-mm analog wafer “fab.” It’s one of six new 300-mm wafer fabs TI is adding to its manufacturing operations. The company said that production will ramp over the coming months to support the future growth of semiconductors in electronics.
Expanding internal manufacturing capacity ‘for the long term’
“We’re thrilled to see initial production running through our newest and largest 300-mm wafer fab, which is part of our investment to expand internal manufacturing capacity for the long term,” Kyle Flessner, SVP, Technology and Manufacturing Group, said in a statement. “This milestone is a result of close collaboration between our construction, facilities, and manufacturing teams and we’re excited to ramp output over the coming months to support our customers’ demand for years to come.”
The company said that the new fab is more than 30% larger than RFAB1, offering more than 630,000 square feet of total clean room space between the two fabs. Inside, 15 miles of automated, overhead delivery systems will seamlessly move wafers between the two fabs once they’re fully built out.
A wafer is a piece of silicon or other semiconductor material that’s designed in the form of a very thin disc. They are used to create electronic integrated circuits and silicon-based photovoltaic cells.
Plants will eventually turn out 100M+ analog chips a day
At full production, TI said the Richardson fabs will manufacture more than 100 million analog chips a day that will go into electronics everywhere—from renewable energy sources to electric vehicles, the company said.
That’s good news in a semiconductor industry that has been battling a prolonged shortage, with the automobile industry hit particularly hard. The shortage sent prices for both new and even used cars soaring, Bloomberg reported.
“Having these two fabs connected within one manufacturing site in Richardson provides great operational efficiencies and scale, allowing us to better support our customers,” Kyle said. “We’ve been in North Texas for more than 90 years and are proud of the great partnership we have with the Richardson community. This is an exciting time for our employees and all of North Texas as we continue to build semiconductor manufacturing excellence together.”
TI said in a statement that it has a long-standing commitment to responsible, sustainable manufacturing and the Richardson fabs are leading the way in that effort.
TI said that RFAB1 was the world’s first LEED Gold-certified (Leadership in Energy and Environmental Design) analog semiconductor manufacturing facility, designed to meet one of the rating system’s high levels of structural efficiency and sustainability. RFAB2, too, was designed to meet LEED Gold standards, building on the company’s sustainability commitment.
Plant is one of six new 300-mm wafer fabs in TI’s pipeline
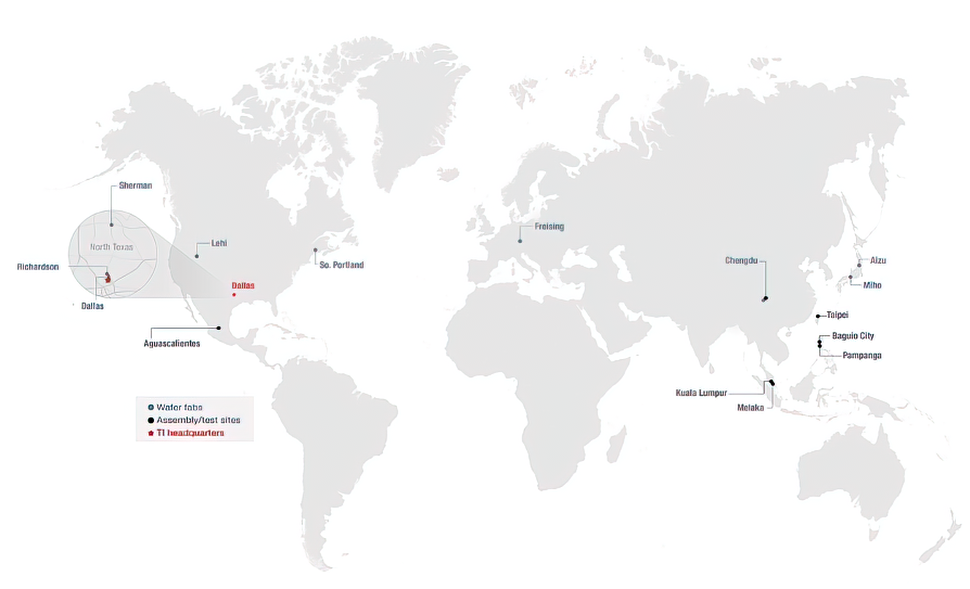
North Texas is a focus for TI’s fab manufacturing. TI has about a dozen wafer fabs, seven assembly and test factories, and several “bump and probe” facilities spanning 15 worldwide sites. Click here for a closer look at the TI’s map.
The company said that RFAB2 complements its existing 300-mm wafer fab footprint, including DMOS6 in Dallas and RFAB1 in Richardson. As one of six new 300-mm wafer fabs being added to TI’s capabilities, the new facility adds to internally manufacture the company’s broad, diverse portfolio of analog and embedded processing semiconductor devices.
LFAB in Utah, which TI bought in 2021, is preparing for initial production in the coming months, the company said.
In Sherman, TI broke ground on its new 300-mm semiconductor wafer fabrication plants (or “fabs”) in May 2022. The potential $30 billion investment looks for four fabs that can “meet demand over time, supporting as many as 3,000 direct jobs,” according to the company. Construction is underway, and production from the first fab is expected in 2025.”
“Our 300-mm wafer fab expansion plays an important role in TI’s future growth and in our ability to support customers’ demand for decades,” Mohammad Yunus, SVP, Manufacturing Operations, said in a statement.
Texas Instruments has a storied history in North Texas
TI emerged in 1951 after a reorganization of Geophysical Service Inc., which was founded in 1930 and manufactured equipment for use in the seismic industry, as well as defense electronics.
In 1954, Texas Instruments produced the world’s first commercial silicon transistor. That’s the same year it designed and manufactured the first transistor radio. In 1958, TI’s Jack Kilby invented the integrated circuit while working at the company’s Central Research Labs.
Texas Instrument invented the hand-held calculator in 1967 and introduced the first single-chip microcontroller in 1970, which combined all the elements of computing onto one piece of silicon.
Get on the list.
Dallas Innovates, every day.
Sign up to keep your eye on what’s new and next in Dallas-Fort Worth, every day.