DesignPlex Biomedical, which designs and manufactures medical devices, has earned an ISO 13485:2016 certification for its Quality Management System. DesignPlex is a client of TechFW, a Fort Worth-based nonprofit that helps entrepreneurs launch tech companies.
The International Organization for Standardization (ISO) developed ISO 13485 because “safety and quality are non-negotiable in the medical devices industry.” It’s meant for organizations that design, produce, install, or service medical devices and related services.
The new version, ISO 13485:2016, was designed in response to new quality management system practices like changes in technology and regulatory requirements.
Certification isn’t a requirement of the standard, but according to ISO, “third-party certification can demonstrate to regulators that you have met the requirements of the standard.”
DesignPlex Biomedical’s certification covers the design, development, and manufacturing of medical devices. That includes active implantable devices for mechanical, electrical, and related software that can be used in the cardiovascular system.
“Becoming certified is an exciting milestone for our company because it provides many great opportunities to create more sophisticated cardiovascular devices that will ultimately help to improve the quality of life for patients,” Robert Benkowski, CEO of DesignPlex Biomedical, said in a statement.
DesignPlex assists organizations and entrepreneurs at every stage of medical device development—from ideation and prototyping to manufacturing a clinical product. Its key areas include: FDA Class II and III medical devices; drug/device combinations; products with electrical, mechanical, pneumatic, and software development; artificial hearts and ventricular assist devices; web-enabled products; and remote monitoring with patient and clinician portals.
Overall, the goal is to bring critical new technology to market commercialization.
The team does it all from an 11,000-square-foot facility, complete with an engineering Design Studio, 3D printing abilities, a dedicated electronics assembly area with ESD flooring, machine shop, mechanical assembly area, polymer room, and quality assurance/quality control offices. They specialize in mechanical design, electronics design, systems integration, and contract manufacturing.
To Benkowski, who is also an assistant professor of Medical Education at TCU and UNTHSC School of Medicine, the ISO 13485:2016 certification means that any product manufactured will now have the traceability, repeatability, and quality that is demanded for Class III devices.
For DesignPlex’s customers, he thinks it will “provide assurance for the formation of a robust design history file” and is now “inherent in how we develop products in a risk-based approach.”
Last year, at the start of the COVID-19 pandemic, we told you about DesignPlex winning a licensing deal—one of only eight manufacturers in the country to do so—from NASA to produce a new ventilator.
Chosen by NASA’s Jet Propulsion Laboratory (JPL), DesignPlex got a royalty-free license to commercialize a ventilator specifically tailored to coronavirus patients. JPL engineers created the prototype in 37 days and received an Emergency Use Authorization from the FDA on April 30.
The high-pressure ventilator, named VITAL (Ventilator Intervention Technology Accessible Locally), was designed to use a seventh of the parts as a traditional ventilator. By using parts readily available in the supply chain, VITAL is a more affordable option for treating critical patients, which also reserves traditional ventilators for those with the most severe COVID-19 symptoms. And, VITAL can be modified for use in the field.
It was up to DesignPlex Biomedical to figure out a way to commercialize the technology.
What’s next? Using the same technique as its polymer left ventricles, pictured below, DesignPlex Biomedical is currently making atrial cuffs and grafts for a new type of artificial heart. The hopes to start clinical studies on the new artificial heart next year, CEO Benkowski says.
GALLERY
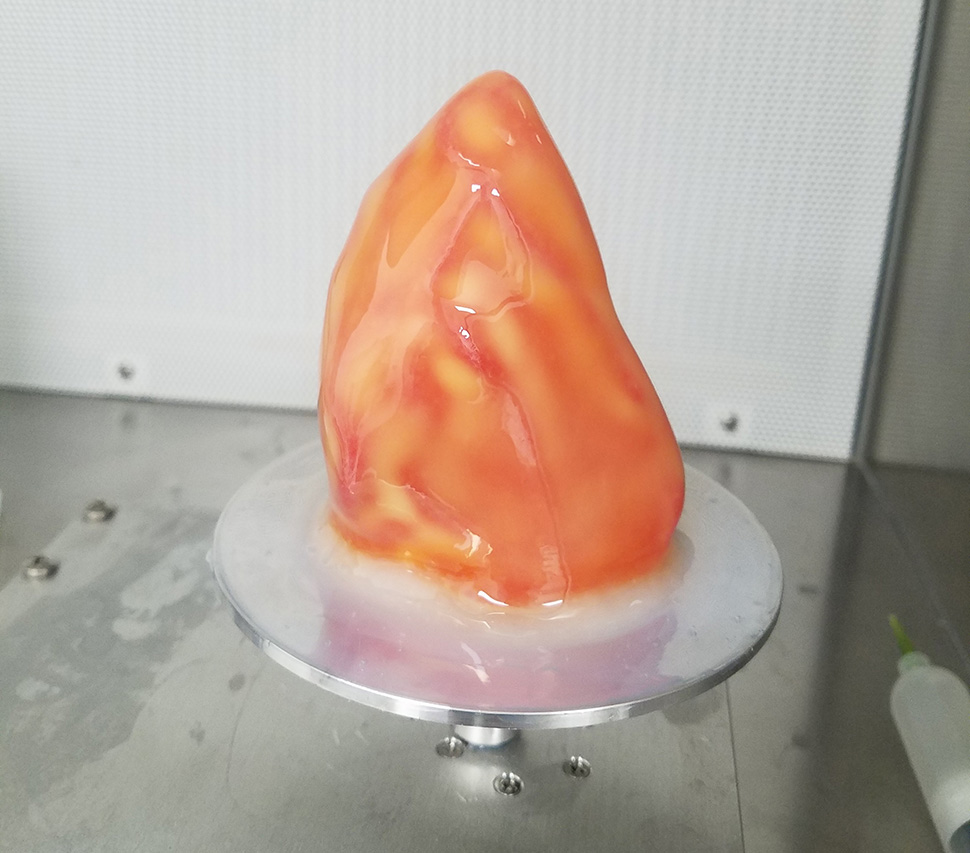
DesignPlex Biomedical developed a left ventricle simulator so its customer could test a minimally invasive pump that resides in the left ventricle. The left ventricle you pictured is taken directly from a CT scan of a human heart with heart failure and the system uses a (human) mechanical mitral valve, porcine aortic valve and runs at 37C degrees so the physiology and flow-pressure waveforms are as close to the human condition in heart failure as possible with the simulator, below.
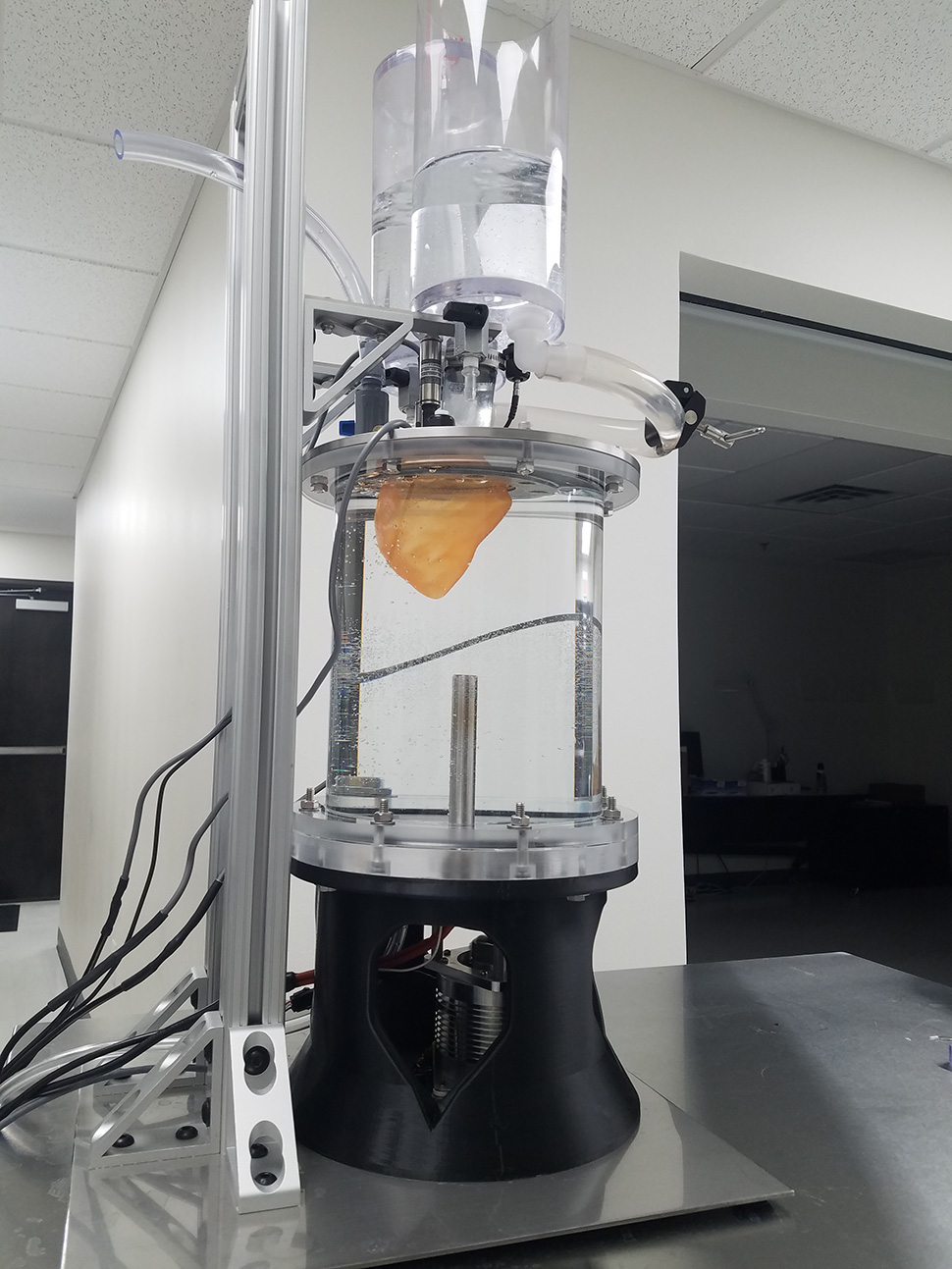
Computer control and hydraulic pressure “squeezes” the left ventricle so it would “beat” and create the flow and pressure an implanted blood pump would see.
Photos courtesy of DesignPlex Biomedical.
Get on the list.
Dallas Innovates, every day.
Sign up to keep your eye on what’s new and next in Dallas-Fort Worth, every day.