As a local startup nears completion of its first proof-of-concept for its 3D-printed homebuilding technology in North Texas, it’s looking to ramp up its efforts across the state.
Dallas-based Von Perry expects to kick off its $2 million fundraising effort on the StartEngine crowdfunding platform. It hopes to use its technology, which uses geopolymer concrete as a material, to streamline the homebuilding process, while making it cheaper and less labor intensive.
“We are bringing in a two-in-one revolution,” Sebin Joseph, Von Perry’s co-founder and CTO, told Dallas Innovates. “We’re bringing sustainability and automation, and we’re also changing the dynamics of the market.”
First home expected to finish in October
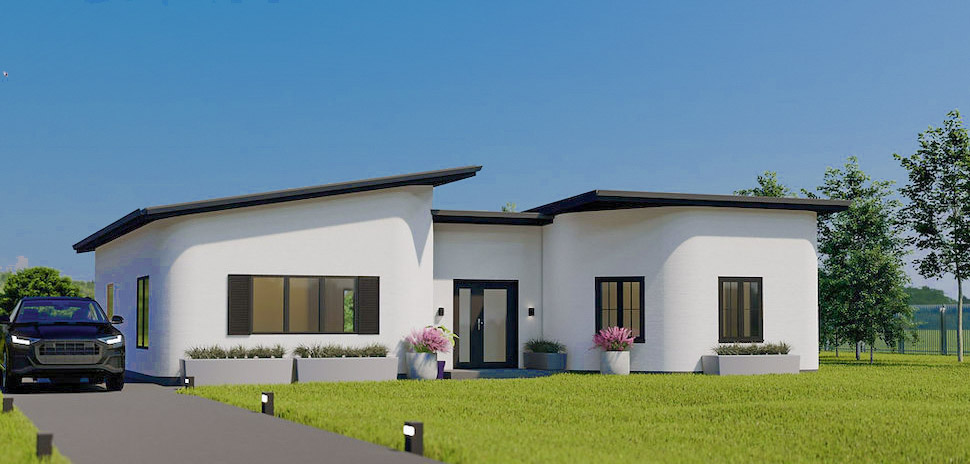
Rendering of Von Perry’s concrete 3D-printed home being built in Nevada, Texas. [Image: Von Perry]
Using hardware from Minnesota-based Total Kustom that requires only a three-person team to operate, Von Perry 3D-prints the structure of custom homes layer-by-layer using the contour crafting method. It’s something that Joseph says can potentially cut the entire construction time of a house down to four months.
“This is going to be the first time anyone builds a house using geopolymer concrete and 3D printing,” Joseph said.
Von Perry didn’t hit that timeline on its initial project in the small Collin County city of Nevada. Joseph attributed the delays to a pandemic backlog in the permitting process and a change from regular concrete to geopolymer concrete to better cope with the Texas heat, requiring a test-build near Austin. But the company expects the 1,700 square-foot, three-bedroom, two-bath house to be completed by the end of October. Initially, the project, which began last December, was expected to be finished by February of this year.
Doubling down in Texas
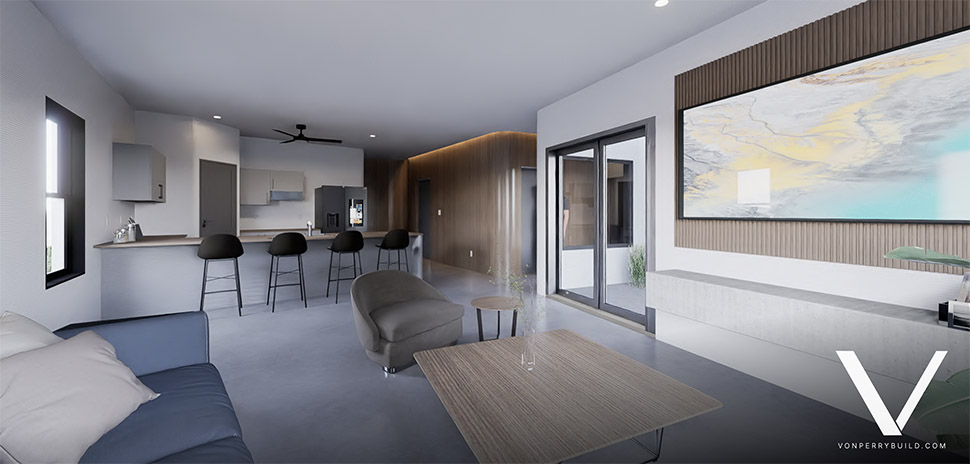
[Rendering: Von Perry]
Despite the setbacks, Joseph said excitement surrounding the project has garnered building requests from around the world. The company instead has decided to double down on its efforts in Texas—where the company’s co-founder and CEO Treyvon Perry previously said codes and regulations make construction easier. Six custom projects are set to come online in the near future, half of which are in Dallas.
“We need to be catering directly to the end user and cut out a lot of middlemen, who actually add a lot of costs to the end product,” Joseph said. “That will also increase the availability of housing in the market.”
To help tackle the new projects, Von Perry plans to crowd-raise the $2 million in funding, which will add to the $40,000 it’s already attracted through UT Arlington pitch competitions. The $2 million is significantly larger than what the company was initially looking to raise when it first began construction on the Nevada, Texas, home.
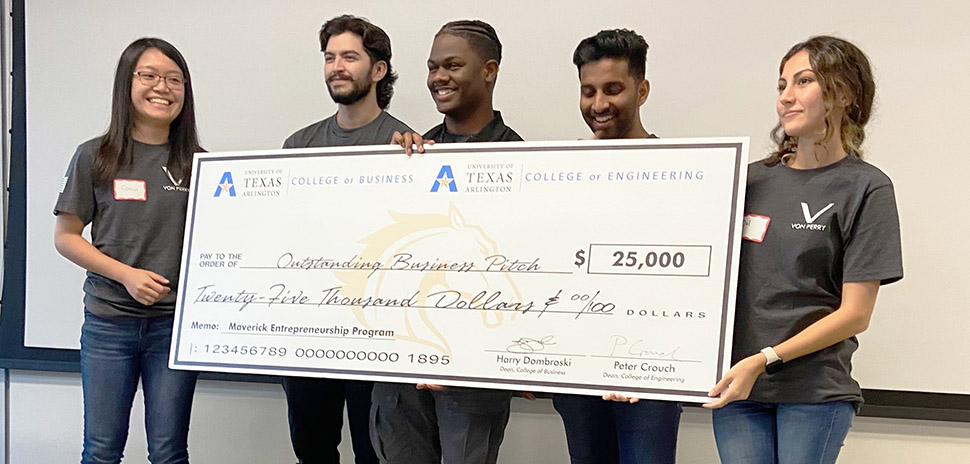
Von Perry team with a check from its victory in a UT Arlington pitch competition.
The ‘core’ software behind the company
The new funding will help the company hire two new construction teams, in addition to helping it launch what Joseph calls the “core” of Von Perry’s business—its proprietary software platform, called Arcus. He said the platform is aimed at “consolidating the entire construction process.” The platform is slated to use artificial intelligence to modify custom home designs, while giving detailed instructions on when and where work needs to be done on a project—so all of the moving pieces on a project fit into place at the right time.
“It will be a streamlined process because they won’t have any kind of confusion,” Joseph said. “(Workers) will get all of the instructions, showing the design where exactly the fixture should be. So they go do that, and they’re done. That way the process will work smoothly. The customer just comes in, makes the order, and they will get that house built without any hassles.”
Interest from defense and space industry
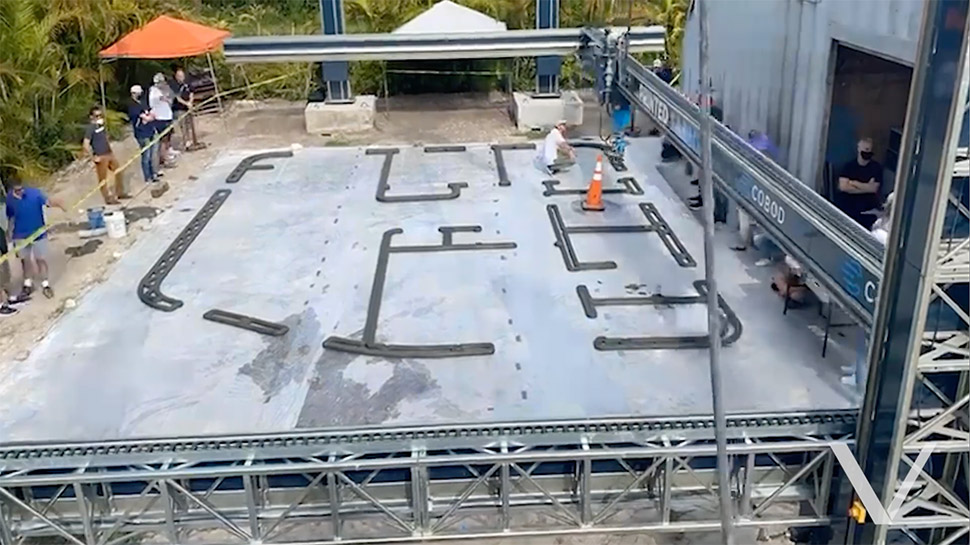
Concrete 3D printing home construction. [Video still: Von Perry]
Outside the custom homebuilding space, Joseph said his company has been receiving interest from players in the defense and space industries—areas the company could potentially consider in the future. He added that some of the funding it raises from its crowdfunding effort will go toward fueling ongoing research and partnerships with UT Dallas, UT Arlington, and UT San Antonio, which in turn are helping supply talent to Von Perry’s nine-person team.
“We are actually building real houses using 3D printers, and that is a jaw-dropping moment for [people]. Because they don’t even believe it is possible. But this is a real thing that’s happening and is slowly revolutionizing the sector,” Joseph said. “We need more investments, more talent poured into this field to make [it] grow and be the mainstream. It will definitely become a mainstream in next 30 years.”
Get on the list.
Dallas Innovates, every day.
Sign up to keep your eye on what’s new and next in Dallas-Fort Worth, every day.