Researchers from the University of North Texas College of Engineering in Denton are participating in a new $1.5 million grant from the U.S. Department of Energy (DOE) to advance the use of 3D printed materials on automotive body frames.
The UNT team will be part of a collaborative effort from the Center for Nanophase Materials Sciences at Oak Ridge National Laboratory, the DOE’s largest science and energy laboratory. The research will be conducted over the next three years in the UNT Center for Agile and Adaptive Additive Manufacturing, according to a statement.
UNT’s Center for Agile and Adaptive Additive Manufacturing (CAAAM) is at the forefront of manufacturing technologies, facilitating the creation of complex, three-dimensional objects with possibilities for far-reaching impacts.
Last year, we told you about how the center, established in 2019, received $10 million in funding from the Texas Legislature to launch. It’s been called one of the most advanced university research facilities in the nation for materials analysis.
Wonbong Choi, a professor in the UNT Department of Materials Science and Engineering and the Department of Mechanical Engineering, and Yijie Jiang, an assistant professor in UNT’s Department of Mechanical Engineering, will conduct the DOE research in the CAAAM.
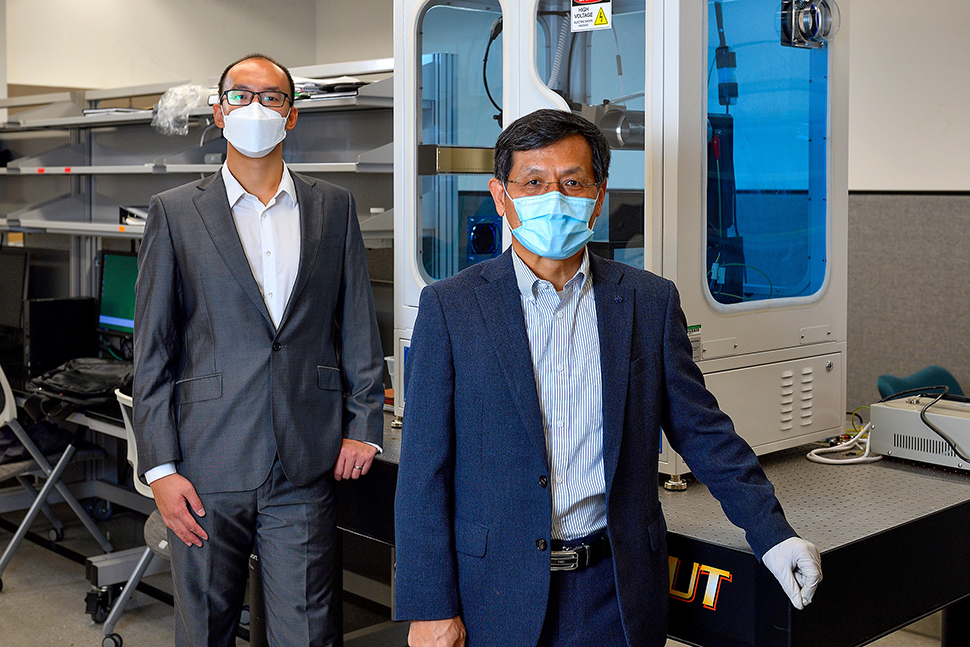
Dr. Yijie Jiang and Dr. Wongbong Choi photographed in their research labs at Discovery Park on the UNT campus in Denton in 2018. [Photo by Michael Clements via UNT]
Both principal investigators for the project, Choi and Jiang received more than $400,000 of the $1.5 million grant to develop “the fabrication of a lightweight, 3D printed carbon fiber composite material equipped with embedded sensors for use in car structures,” according to UNT.
“Once we have developed and successfully tested materials, we can provide stronger, safer and more lightweight options for automotive additive manufacturing,” Jiang said in a statement. “Readily available, proven materials will provide opportunities to lower costs and advance the industry.”
Inside the research
Traditionally, car frames are mass produced.
The process uses subtractive manufacturing, in which shapes are cut from a sheet or slab of material and then molded into parts, the researchers said. Once these shapes are cut, any leftover material is discarded or recycled for reuse.
This creates waste and additional cost. With additive manufacturing, researchers say, that can be eliminated.
Instead of cutting away materials, additive manufacturing uses data computer-aided-design software or 3D object scanners to deposit material in shapes and intricate designs.
According to UNT, Choi and Jiang will evaluate materials that use flexible micro sensors embedded into the material and located precisely during 3D printing. During the testing phase, these materials should deliver real-time performance data.
Once a material is proven successful, it can be installed in cars. Embedded sensor technology will then provide dashboard data for car owners, which is comparative to current sensor tech that notifies a driver when fuel or tire pressure is low.
The embedded sensors will be able to identify and provide alerts for issues in the car structure, according to researchers.
The UNT team hopes this will prove 3D printing technology can improve performance and produce complex structures with simplified fabrication. It’s not currently an option considering the lack of readily available materials and more affordable mass production options.
“Prestigious labs from all over the country submitted proposals to participate in this DOE collaboration with Oak Ridge National Laboratory,” Choi said in a statement. “Our selection is a testament to the innovative research and industry collaboration CAAAM provides. Through this grant we will advance materials and technology available to industry, offer students hands-on experience in the field and elevate UNT’s status as a Tier One research university.”
Get on the list.
Dallas Innovates, every day.
Sign up to keep your eye on what’s new and next in Dallas-Fort Worth, every day.