Plano-based Siemens Digital Industries Software announced that Maeve Aerospace B.V. has adopted the Siemens Xcelerator portfolio of industry software and services to aid in the development of Maeve 01, the company’s next-generation, zero emissions all-electric passenger aircraft.
Maeve 01 was unveiled this week at the Paris Air Show. It enables more than 44 passengers to travel in a range of 250 nautical miles with zero emissions.
“Maeve’s experienced aviation team having the Siemens Xcelerator portfolio of design and simulation tools in their toolbox has given us the perfect opportunity to take our electric aircraft design to the next level,” Joost Dieben, Maeve’s co-founder and chief commercial officer, said in a statement. “Maeve is empowered with these tools and Siemens’ expertise has helped us to get one step closer to zero-emission aviation. Together with Siemens, we’ve been able to accelerate our development process to be able to start flying before 2030.”
Maeve, which is headquartered in the Netherlands, said its mission is to transform regional air mobility, guided by a commitment to mitigate environmental impact.
Maeve seeks to significantly decrease emissions and energy consumption with its all-new electric aircraft design while improving the aviation industry’s economic and social prosperity, building a sustainable future that contributes to a healthier planet for future generations.
Pioneering zero emission flights
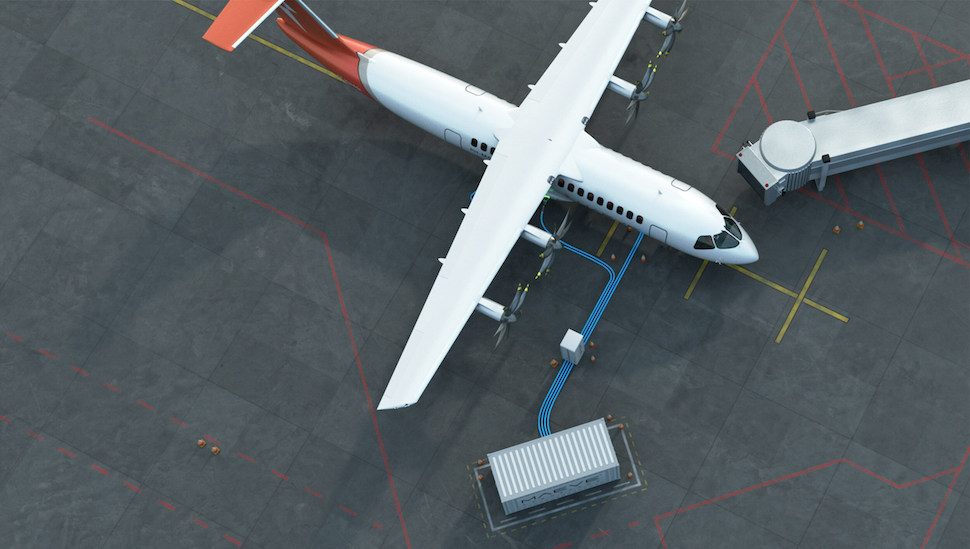
The all-electric Maeve 01 juices up. [Photo: Siemens Digital Industries Software]
Maeve said its growing team of aviation experts is pioneering the path towards zero emission flights.
Recently, it received global interest from investors including a conditional investment of €17.5 million co-investment from the European Innovation Council and over €2.5 million in Dutch grants.
Maeve said that under the technical leadership of its new chief technology officer, Martin Nuesseler, the company’s team has redesigned and optimized its earlier aircraft using the Siemens Xcelerator portfolio of industry software.
The company said that creating a digital twin of its all-electric powertrain and executing full thermal and safety simulations on its in-house designed aircraft dedicated battery system have enabled it to significantly reduce the aircraft’s overall weight. That resulted in the reduction of aircraft structures, delivering an increase in propulsion and battery capacity, Maeve said.
Compared to existing turboprop aircraft, Maeve 01 reduces operating costs by 30%, the company said.
“Maeve, like many aerospace industry innovators, is adopting Siemens Xcelerator as the platform of choice for the development of next-generation vehicles,” Todd Tuthill, VP, aerospace and defense, Siemens Digital Industries Software, said in a statement. “To meet market demands, sustainability requirements and remain competitive, aerospace companies need new ways to deliver products faster and Siemens’ goal is to help our customers push the boundaries of innovation while making digital transformation easy, fast, and at scale.”
Innovation in digital transformation—and a recent TIME100 honor
Siemens Digital Industries Software said it helps organizations of all sizes digitally transform using software, hardware, and services from the Siemens Xcelerator business platform. Just this week, Siemens was named to the TIME100 Most Influential Companies list with its Xcelerator as a driving reason.
Siemens’ software and the comprehensive digital twin allow companies to optimize their design, engineering, and manufacturing processes to turn today’s ideas into the sustainable products of the future, the company said.
Siemens Digital Industries said that it is an innovation leader in automation and digitalization, closely collaborating with partners and customers to drive digital transformation in various industries.
Siemens Digital Industries has its global headquarters in Nuremberg, Germany, and has around 76,000 employees internationally.
Get on the list.
Dallas Innovates, every day.
Sign up to keep your eye on what’s new and next in Dallas-Fort Worth, every day.