We’ve all seen companies in a myriad of industries step up to begin producing personal protective equipment during the COVID-19 pandemic. But for Deep Ellum-based MedCAD, custom medical devices are its bread and butter—meaning the team’s expertise and resources could easily lead to innovation for a healthcare crisis that doesn’t yet have an end in sight.
When the coronavirus outbreak and subsequent shelter-in-place began, the team at MedCAD began receiving calls from their network of surgeons and sales reps across the country. Running on short supply, many were reaching out in need of PPE and other devices.
MedCAD was ready and eager to step up where traditional manufacturing methods would falter. Biomedical engineering and rapid prototyping (a custom device can be finished in three days post-consult sometimes) is built into the company’s DNA.
“We have been able to pivot well to this challenge,” Marketing Manager Parker Smith says. “Our engineers love a challenge, so with a lightened caseload due to the deferral of elective surgeries, they were eager to jump in and help.”
Reusable face shields came first, as MedCAD wanted to contribute to the open source movement and there was the largest need for that at the beginning of the pandemic. It was also the device with the fastest turnaround. An open source design has even already been internally improved and is available for download and ordering.
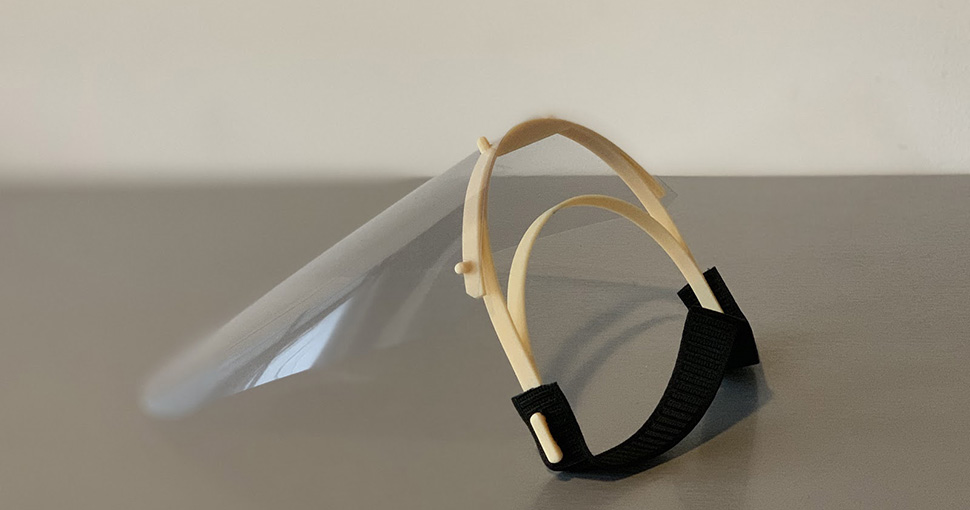
MedCAD’s shields can be printed (optimized for resin printers) from the design on its website. The team is also what 3D printing a significant quantity to give away for free and taking bulk orders. [Image: Courtesy MedCAD]
“Some of the feedback we’ve gotten is that face shields are really the important pieces right now because of the particulate of the COVID disease,” MedCAD’s CEO Nancy Hairston told Dallas Innovates. “So we’ve taken some time to iterate on a design on the headband. It’s been about three weeks, and we’ve actually started shipping those out this week.”
Now, the team, which is under 50 people, is tackling ventilator valves and other PPE that are in short supply at hospitals—and working to make them better than is already available.
MedCAD sets out to build PPE. But better.
Currently in the prototyping phase are reusable filtered face masks and other open source accessories like “Ear Savers.” MedCAD is exploring breathing devices, too: Ventilator valve splitters allow hospitals to support multiple patients with a single ventilator and valve filters to lower the risk of airborne virus transmission.
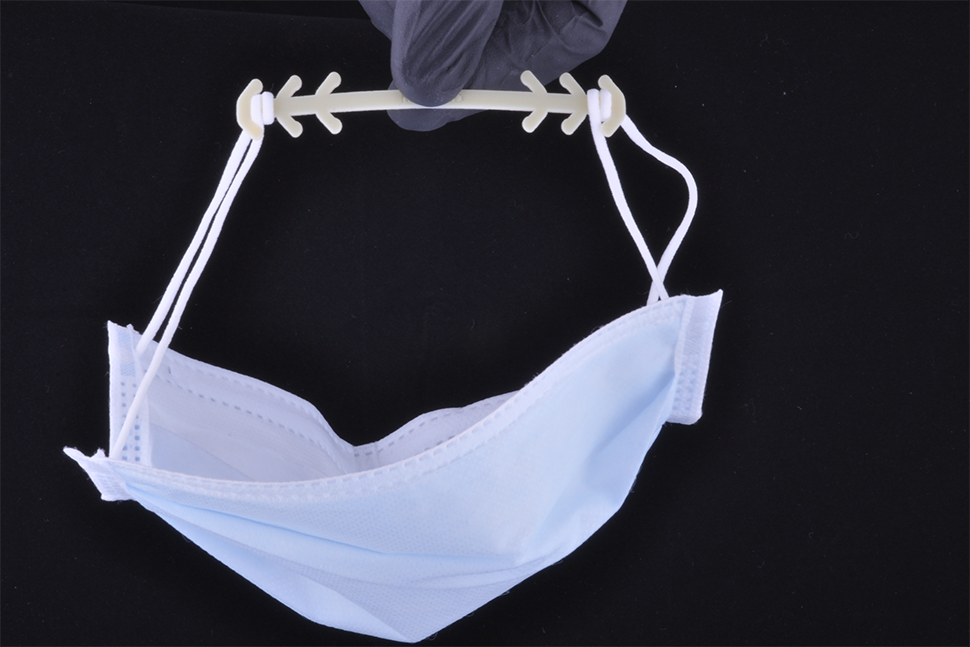
[Image: Courtesy MedCAD]
To make a mask N95, it needs to have a strong seal around the face, Hairston says. She’s seen the horror stories and photos of healthcare workers wearing the masks currently available, and continuously heard people wondering if a “better mousetrap” could be made.
That’s primarily why MedCAD doesn’t have a mask out yet. What’s being created is something totally novel and new.
“This mask technology is very, very old. This is an opportunity to innovate. That’s what we’re after,” Hairston says. “Being a custom device company and having such talented engineers in the company on the N95 mask side, we’re not looking to just sort of output something quickly.”
MedCAD is now on version 16 of its mask prototype. Hairston’s aspirations aren’t small—she wants to take the PPE currently out there, evaluate, and make it better.
“In a hospital setting, clean, filtered air is required for caregivers because of the concentration of patients with the disease. So there’s a challenge to make a mask that filters sufficiently while being comfortable for the caregiver,” she says. “Reusable would be a plus. These are the kinds of needs we’re considering in the design process.”
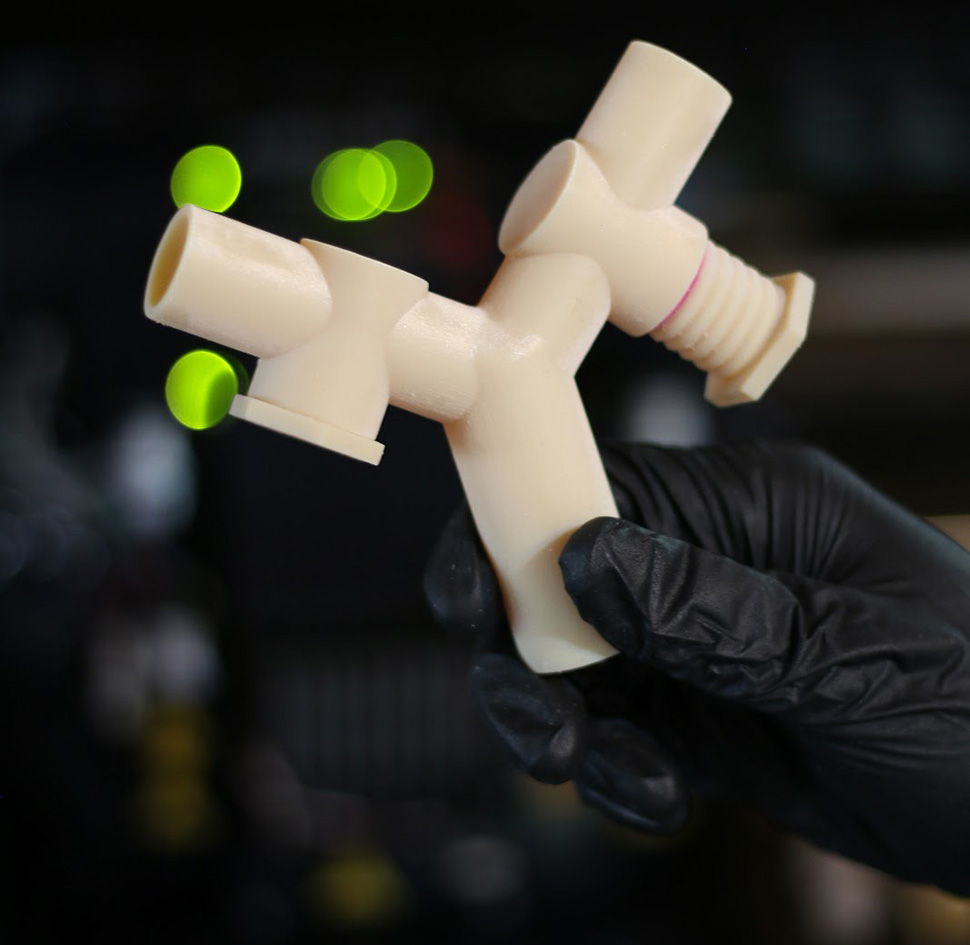
[Image: Courtesy MedCAD]
Behind the scenes at MedCAD
Pre COVID-19, MedCAD primarily focused on custom medical devices and manufacturing custom implants for neurosurgery and 3D-printed accessories for corrective jaw surgery and reconstruction. The team works on a case-by-case basis, which could be anything from a car accident to a traumatic brain injury to cancer.
“Our secret sauce is in the service we provide. We have software we’ve developed in-house that gives us the ability to not only customize a case, but customize everything we do for a surgeon. And we can do that immediately,” Hairston says. “They know when they work with us, they have a security blanket that the approach is going to be the same every time.”
MedCAD, founded in 2010, has a manufacturing facility equipped with a fleet of high-volume 3D printers, mills supported by a team of biomedical engineers and quality assurance, and installed a nearby lab at Texas A&M Health Sciences last fall. The new lab is meant to provide a turnkey solution for healthcare professionals to access the power of CAD and 3D printing without having to become a biomedical engineer.
Given the national quarantine, most of MedCAD’s cases, since they’re primarily elective surgeries, are delayed until May-June. For the time being, most resources have been repurposed to make the protective gear, though the company is still continuing new product development.
“In our company, we have this sort of dichotomy of rapid prototyping, rapid production, and custom design that’s quick and iterative, combined with medical devices, which are very slow and careful,” Smith says. “So our creativity is complemented by a very strong quality system, which makes sure that the things we work on are in line with FDA regulations.”
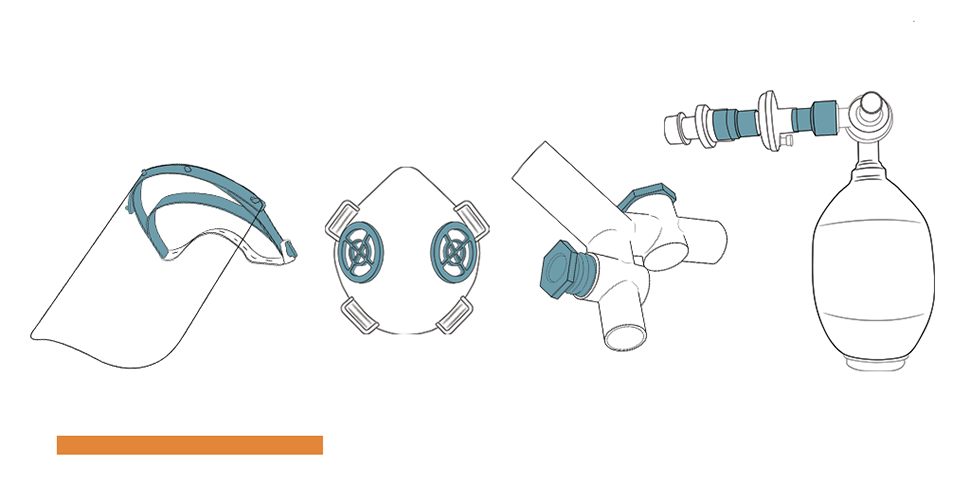
[Image: Courtesy MedCAD]
MedCAD’s regulatory team is diligently working to ensure all products—even with the FDA Emergency Use Authorizations—comply with safety standards. And, figuring out which product fits with MedCAD’s already available technology.
“If you’re making a ventilator valve, you need high accuracy,” Hairston says. “So we actually use dental printers for those, which in our normal course of business would print a temporary crown. It just depends on the job that we’re going after and figuring out which printer is better for that job.”
Once completed, a substantial amount of PPE will be given away pro bono, although MedCAD has already received a number of bulk pre-orders. Smith says a large number of products will help North Texas facilities, too.
“PPE is in short supply. You can hardly get protective gear at your local hardware store, so we’re hoping to fill a void locally. And not just for medical professionals in hospitals—but for first responders and retailers as well,” he says. “Our donations of PPE will help keep people safe.”
And MedCAD knows its job doesn’t stop here. Hairston plans on continuing her customized approach to see what innovations could solve the new situations that arise every day.
“We’re looking at how to produce products that we never dreamed we might go for in the past,” she says. “This problem could be around for the next 18-24 months. As a nation, we’re in this for the long haul. So I think if we can develop some new ideas, we’re definitely teed up to do that.”
Get on the list.
Dallas Innovates, every day.
Sign up to keep your eye on what’s new and next in Dallas-Fort Worth, every day.