A North Texas rocket company is flying high thanks to a new award that will boost its breakthrough propulsion projects. Addison-based Firehawk Aerospace announced Wednesday that it’s been selected by AFWERX for a SBIR Phase I award focused on the development of solid rocket motors and hybrid rocket engines for the U.S. Air Force.
AFWERX is an Air Force program that aims to foster a culture of innovation by streamlining the development of new technologies—helping companies like Firehawk cut through the red tape to advance their projects.
Firehawk Co-Founder and CEO Will Edwards said in a statement that his company’s “unique approach” to fuel production allows it “to quickly design and test solid rocket motors and hybrid rocket engines, enabling the potential for large-scale production of our motors for a variety of systems both domestically and internationally.”
Firehawk said it “remains dedicated to solving the supply chain problems that plague the propulsion industry” and added that the SBIR Phase I award will help accelerate its mission.
Aiming to be ‘the next great American defense company’
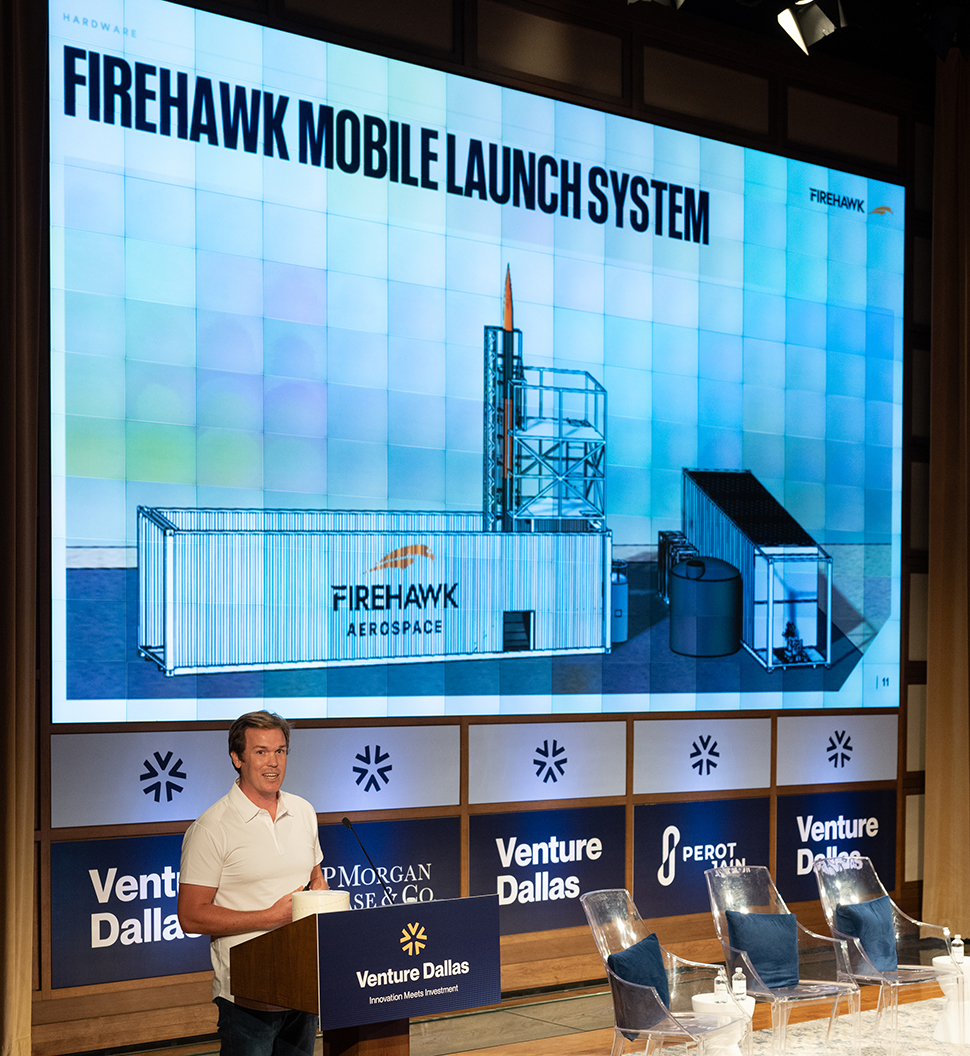
Will Edwards speaking at the Venture Dallas Summit in October.
In October, Edwards spoke at the Venture Dallas Summit at the George W. Bush Presidential Center, where Firehawk was named one of three Startup of the Year winners. At the summit, the CEO set out a big goal for his company.
“Our motto is to build the next great American defense company. And we’re doing this by building rocket motors,” Edwards said.
“If you look at the industry today, it’s extremely hard to build a rocket engine. One of the biggest supply chain cruxes that we have is producing the rocket fuel,” he added, noting that it can take “up to 15 to 60 days” just to produce it.
“The way we produce rocket fuel right now for missiles—or even for satellite launchers—is you dump all the ingredients into a mold, you let it dry. And because you’re essentially building a bomb to propel another bomb, it goes through extensive quality control.”
“Talk to anyone, the CEO of Raytheon… They say rocket motors are the bane of their existence; it’s a critical asset that we cannot meet,” Edwards said.
Then he held up Firehawk’s solution on the Venture Dallas stage: an example of its 3D-printed solid rocket fuel.
‘Secret sauce’ cuts rocket fuel production time from up to 60 days to just 7 hours
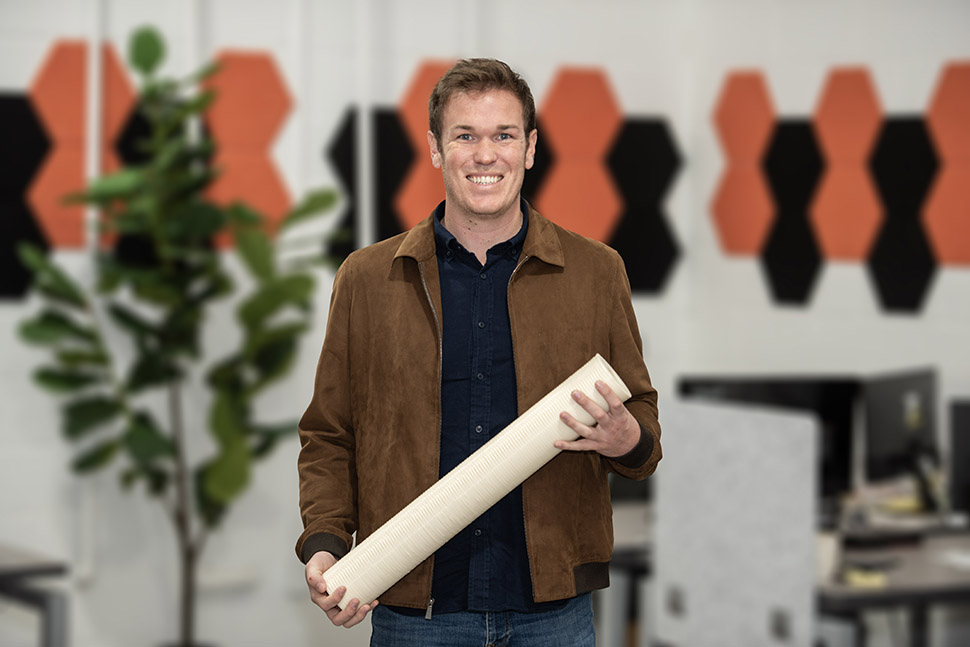
Firehawk Co-Founder and CEO Will Edwards holding a sample of his company’s 3D-printed solid rocket fuel. [Photo: Michael Samples/Dallas Innovates]
“This is actual rocket fuel right here,” he told the audience. “What Firehawk found out was if you 3D-print rocket fuel, you can actually produce fuel using a chemical formulation that’s incredibly safe.”
Not only safe, but faster, too, he added.
“We’re taken production down to just seven hours. Quality control is part of the print process. The curing time is part of the print process. And I do it all out of my facility in Addison, Texas.”
As to costs? Edwards compared Firehawk’s “$170,000” 3D printer in Addison to companies like California’s Aerojet Rocketdyne, which he said was given “a quarter billion dollars by the government just to build a facility where they can produce rocket engines for three systems.”
Edwards waved that away with a gesture at his rocket fuel sample. “At the end of the day, this is our secret sauce,” he said. “What we sell is an actual rocket motor. And we have a lot of a lot of benefits to our engine because of our 3D printing. It’s 1/10 the price of what’s out there today. It’s nearly environmentally benign, incredibly safe.”
Capability of fast turnarounds, with five awarded patents
In December, Firehawk was selected by the Army Applications Laboratory as a supplier for the Javelin, Stinger, and GMLR System.
Edwards has noted that Firehawk’s solution is modular, enabling him to design “overnight” an engine for rapidly-depleting hardware like a Stinger anti-air missile or a Javelin anti-tank weapon system.
Once designed, they “can be tested at our facilities in a matter of a few months,” he said.
One capability of his rocket engine is its ability to be turned off in mid-flight, allowing the system to go through a glide phase, instead of quickly depleting its fuel in one go.
“Because of that, we have enhanced maneuverability,” he said. “We can fly farther and we can direct our energy more efficiently.”
Edwards added that Firehawk is building its own mobile launch system. As to IP, he said his company has been issued five patents on its technology—”the 3D printing of rocket fuel, adding metal additives to it, adding different vortex designs”—and has filed for “several more” patents as well.
A fruitful 2021 relocation to North Texas
Firehawk relocated to North Texas in early 2021 from its former home in Melbourne, Florida, and has found fruitful ground for fast growth here.
“Ever since one of my first phone calls with Capital Factory, and I decided to relocate to North Texas, great things have happened,” Edwards said in October on the Venture Dallas stage. “We became Raytheon’s first-ever venture investment. We’ve signed millions of dollars in defense contracts, raised a [$17.6 million] Series B—and a majority of that came from the Texas North Texas ecosystem. We won appropriations.”
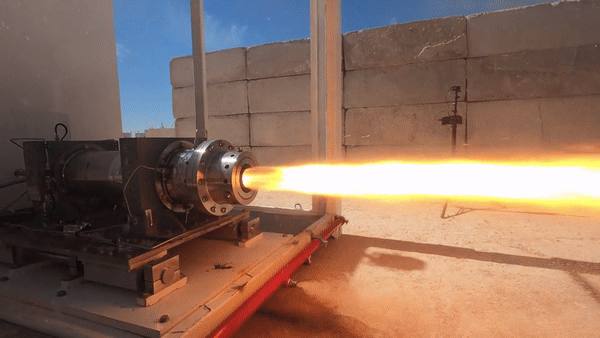
Firehawk tested its engines in a “big hot fire” in March 2023. [Video: Firehawk; Gif DI Studio]
Firehawk’s Texas presence extends as far west as Midland, Edwards noted, and continues to grow.
“We have 42,000 square feet in Addison where we can design print our fuel, build our engines, build the mobile launch system,” he said. “We have a couple of acres in Midland, Texas, where we’re testing everything. We’re about to take over several square miles to build out our own launch range. Us and Jeff Bezos all have our own private ranges.”
Firehawk officially announced in November the development of a 30-square-mile launch range in West Texas for its hybrid rocket testing.
‘Outside issues can’t slow us down’
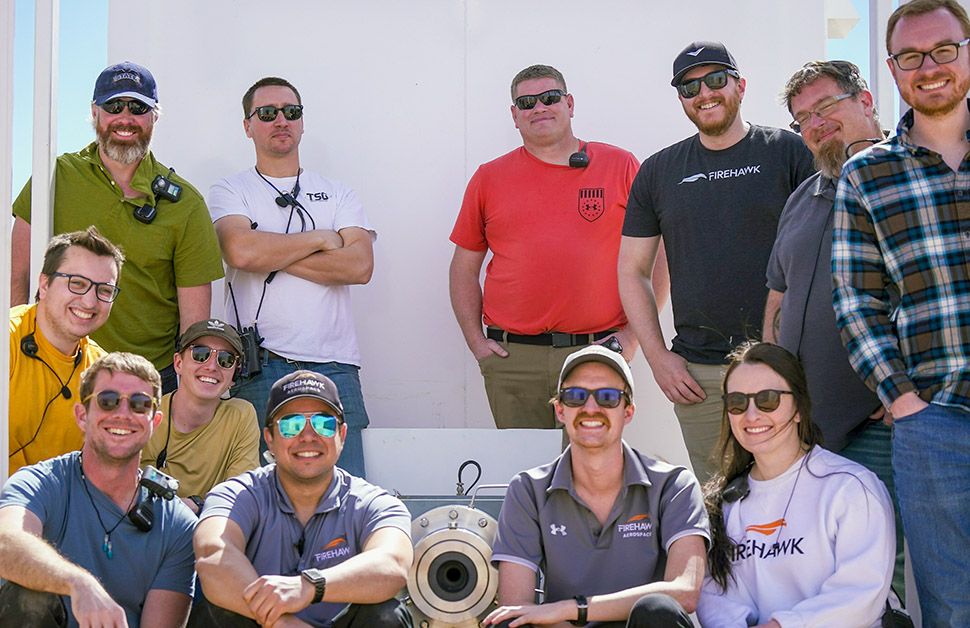
Firehawk Aerospace team at their Midland, TX, rocket engine test site. [Photo: Firehawk Aerospace]
The AFWERX SBIR award is designed to speed things up, which is fine by Edwards, who notes nonetheless that “outside issues can’t slow us down.”
“Now Firehawk can design our engines at our own facility, test it at our own facility, and fly it at our own facility,” he explained. “We want to move as quickly as possible for the customer.”
Helping Edwards speed the process is his team—including Chief Technology Officer Justin Karl, formerly a technology advisor at E2MC Ventures and a lecturer and TP Chair at the International Space University, and Chief Engineer Edward Mader, formerly chief engineer at L3 Harris Technologies and a senior member of the technical staff at Sandia National Laboratories.
“Everyone else comes from Lockheed Martin, Boeing, Blue Origin—we pulled them from some of the best companies,” Edwards said at Venture Dallas. “And they are very excited to move to Dallas, to say the least.”
Streamlining award timelines, eliminating bureaucratic overhead
For now, Firehawk is taking its AFWERX SBIR 1 award and running with it—and as Edwards hinted at Venture Dallas, “a big Army contract” could soon be forthcoming as well.
Firehawk noted that the Air Force Research Laboratory and AFWERX have partnered to streamline the Small Business Innovation Research (SBIR) and Small Business Technology Transfer process. The goal is to accelerate the experience of small businesses like Firehawk through faster proposal to award timelines, changing the pool of potential applicants by expanding opportunities to small business, and eliminating bureaucratic overhead by continually implementing process improvement changes in contract execution.
Get on the list.
Dallas Innovates, every day.
Sign up to keep your eye on what’s new and next in Dallas-Fort Worth, every day.