Home construction is one of the oldest industries on earth. Now two of the sector’s youngest co-founders plan to write a new chapter—by building a concrete 3D-printed home northeast of Dallas, the first to be built in North Texas.
Treyvon Perry, the 21-year-old co-founder, CEO, and lead designer of Von Perry LLC, and Sebin Joseph, his 27-year-old co-founder and CTO, are pioneering a process that’s only begun to emerge in the U.S.
Methods and standards are evolving with every project. Until now, homes built with concrete 3D printing have required highly engineered concrete that can cost as much as four times the price of the regular kind.
But Von Perry plans to build what it says will be the first such home in the U.S. using something you walk on every day—regular, locally sourced concrete.
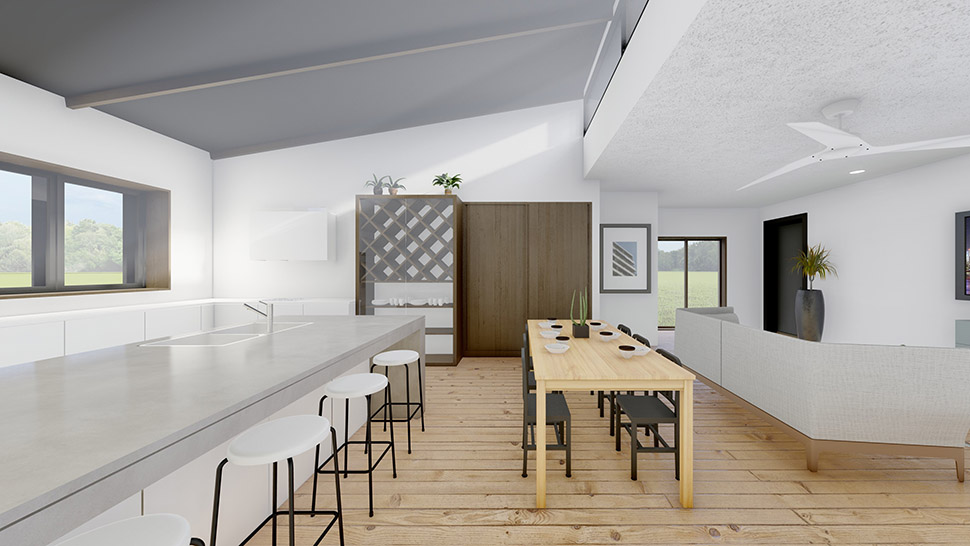
Rendering of the Nevada, Texas, home’s interior. [Image: Von Perry]
Aiming to build a 1,700-SF, 3-bedroom home for $120 per square foot
To print its “v-Home,” the startup will use a huge, foldable gantry system trucked down from Minnesota-based Total Kustom, featuring the company’s Stroybot concrete printer.
Perry believes the cost savings of regular concrete will help his startup build the home for around $120 per square foot. The 1,700-square-foot, three-bedroom, two-bath home will be built near the small town of Nevada, east of Lake Lavon in southeastern Collin County, at a projected cost of $200,000 to $220,000.
Von Perry is one of the few early-stage startups taking this tech directly to home buyers.
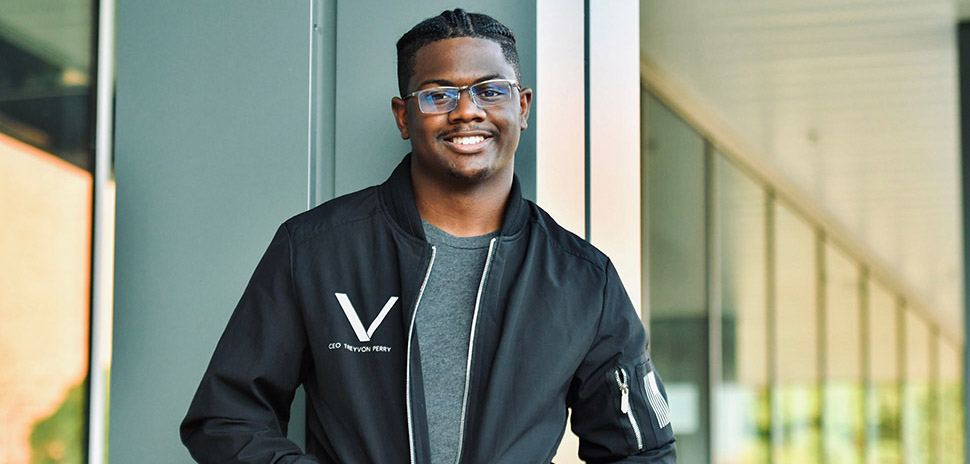
Treyvon Perry, co-founder, lead designer, and CEO of Von Perry. [Photo: Von Perry]
Small town, fewer code hurdles
Nevada is a small town—population 822 in the 2010 census—which is helping Von Perry pull this off. They haven’t had to deal with standard city building codes, as they would in a big city like Dallas. Instead, they obtained permission from the Collin County engineer.
Why Nevada? One of Von Perry’s team members had a relative who owned a lot there and wanted to build a home.
“They were looking for an affordable option,” CTO Sebin Joseph told Dallas Innovates. “The idea came up, we pitched it to them, and they liked it.”
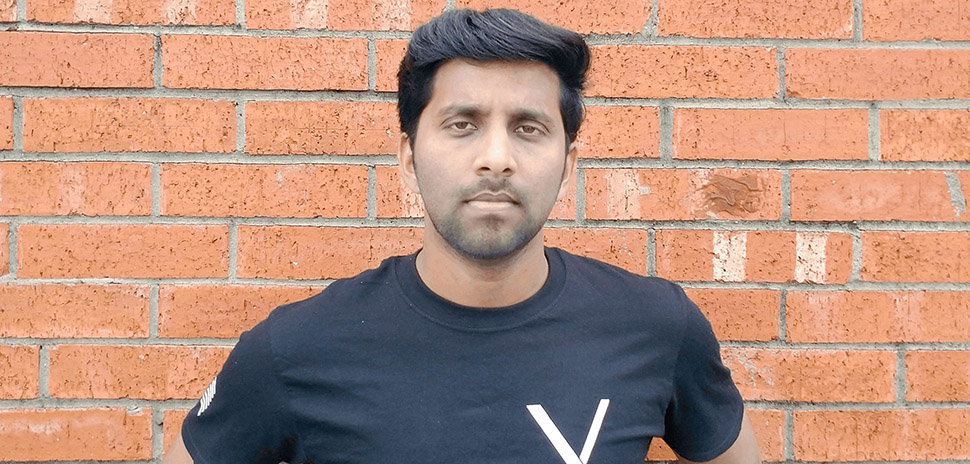
Sebin Joseph, co-founder and CTO of Von Perry. [Photo: Von Perry]
The house is slated to be finished in early 2022. The founders say they already have nine clients lined up after it’s completed. “So even before the house is built, we’re getting a lot of interest from just this one project,” Joseph said.
Still a UTA student, the CEO has worked toward this for years
CEO Treyvon Perry may only be 21, but he’s spent nearly four years working toward this date with construction history. He founded Von Perry as a 17-year-old while attending a 3D technology center in Garland. His goal: create a company that could deliver “nice architectural impact, but also bring a lot more affordability.”
He went on to attend UT Arlington, where he’s currently a third-year architecture student. While at UTA, he’s been an event coordinator for the architect student institute AIAS and a social media coordinator for the U.S. Green Building Council.
He also discovered the concept of 3D-printed homes.
“I felt like this was something that could be huge,” Perry told Dallas Innovates. “The market’s brand new, and it’s something I believe we could bring instantly to DFW.”
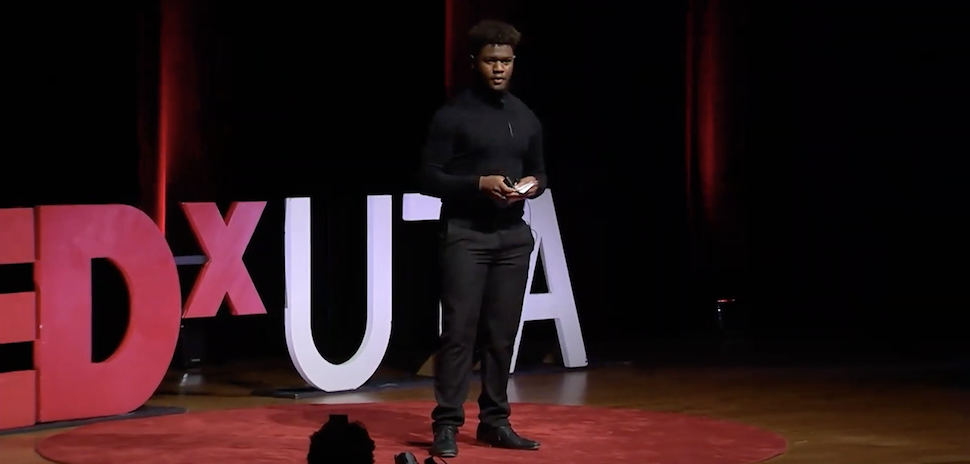
Von Perry co-founder and CEO Treyvon Perry speaking at TEDxUTA in 2020. [Video still: TEDxUTA]
In 2020, Perry gave a TED talk at TEDxUTA on 3D-printed homes. Then he put out a LinkedIn call-up for a CTO to help launch Von Perry formally.
“Literally within the first hour or so I had 50 submissions,” Perry said. “And Sebin popped up as somebody who was very passionate in the belief and the goal of the company. Ever since then, we’ve just been clicking and hitting our goals non-stop.”
The co-founders incorporated Von Perry last April. They’ve since built their team to seven people, with plans to hire four more by the beginning of 2022.
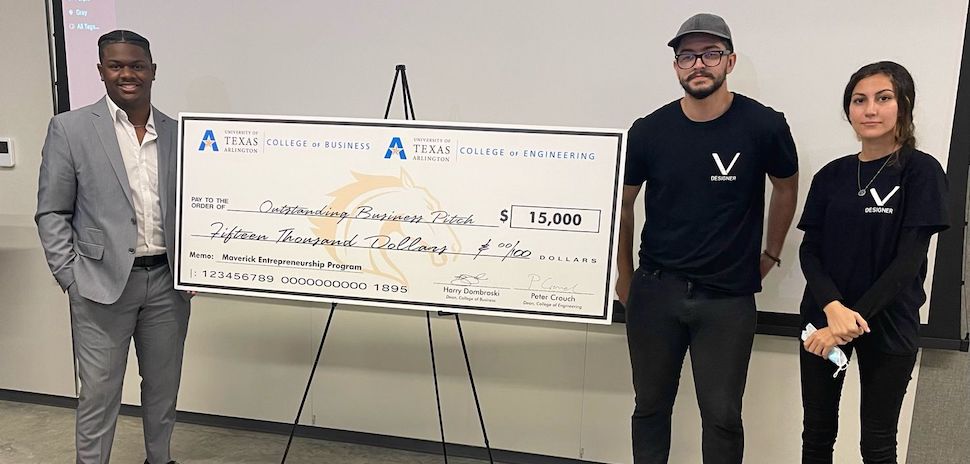
Von Perry won a recent MAVPitch competition at UT Arlington. Shown are CEO Treyvon Perry, left, with Von Perry designers Gerardo Alvarez and Dal Thibian. [Photo: LinkedIn]
Von Perry recently won a MAVPitch competition at UTA
In another recent boost, Perry and his team won first place at a MAVPitch competition from the Maverick Entrepreneurship Program at UT Arlington.
The win came with the $15,000 prize seen above.
Perry likes to pitch the benefits of concrete 3D printing. The strong, heavy walls it creates hold up much better against storms, fire, and water damage. They also provide a lot more design freedom. Curved walls and straight walls can be created for the same price, allowing the architect’s fluid vision to be realized without a leap in costs.
How concrete 3D printing works
The home in Nevada will begin with a standard slab foundation. After that, the usual stick-and-brick framing process is replaced with concrete 3D-printed “contour crafting.” The huge gantry system from Total Kustom will robotically pour an inside and outside layer of concrete for each wall, 12 to 16 inches high at a time. After one layer dries, the next vertical layer is added until the walls reach 10 feet high.
The cavity between the two concrete wall layers leaves space for insulation, plumbing, and electrical lines—as well as concrete beams which will be poured later to support the roof framing.
Only three people are needed to run the 3D printing system—saving the startup a lot of money in labor costs. Joseph says the printing process will take about a week.
Less need for finishing
Many home construction costs happen in the finishing—adding the drywall, taping and bedding, texturing and painting, etc. But Joseph says that’s not even required for 3D-printed concrete walls.
“You don’t even have to paint it. It can still look very aesthetically pleasing,” Joseph said. “And you have the option of smoothing out the lines in the wall to make it look like sheetrock. Some people don’t care about the lines.”
The client in Nevada northeast of Dallas has requested the wall smoothing option, along with a surface layer of stucco.
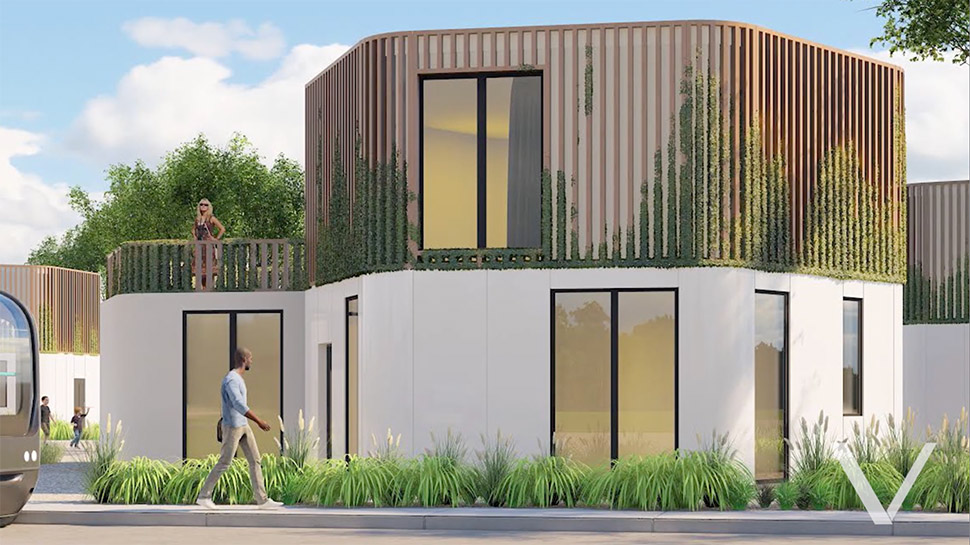
Rendering of another Von Perry-designed concrete 3D printed home. [Image: Von Perry]
Hoping their test case house will lead to wider acceptance
When finished in early 2022, the Collin County house will serve as a “livable, real house” test case for the 3D printing process.
“It will be a lot easier to build a home like this across the country if we have proof of concept with this Nevada project,” Perry told us.
“There are only a dozen or buildings [like this] in the entire world,” Joseph added. “Everyone is using their own methods of construction, according to the local laws and their structural engineers’ recommendations. We’re doing the same thing. Every time you do a new building, you will learn a lot of stuff.”
That’s one reason it could be more difficult to build a 3D-concrete-printed house in a city like Dallas
“Construction is a very old industry, perhaps the oldest industry in the world,” Joseph said. “So when you introduce a new technique into that already existing norm, there’ll be huge resistance. We’re also facing that.”
The founders hope their Nevada project will prove the quality and benefits concrete 3D printing can deliver.
“This approach is pioneering because it leads the way for a lot of other products in the Dallas area,” Perry said. “As far as building codes, it’s going to be hard to fight. The whole industry is fighting through that as well. But I wouldn’t say it’s impossible.”
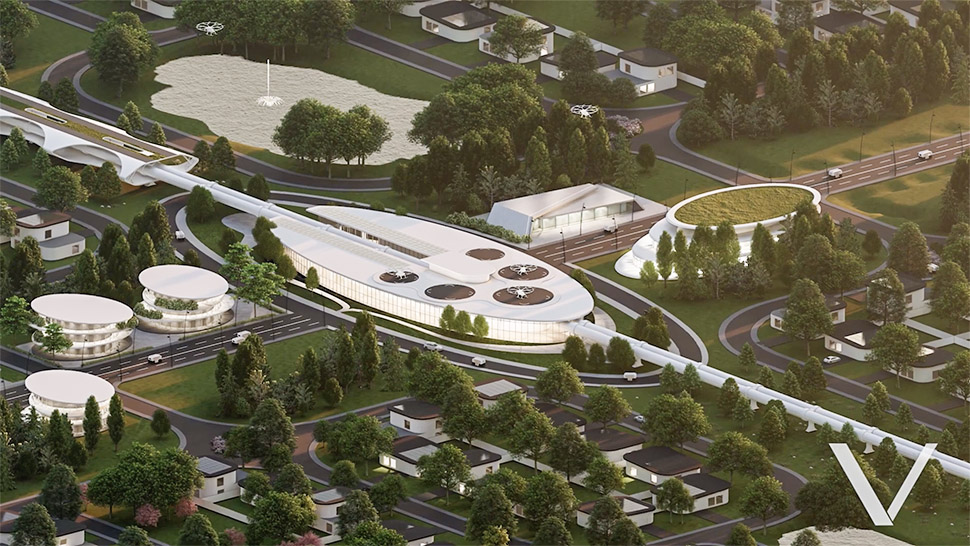
Von Perry thinks big with this rendering of the possibilities of concrete 3D printing. [Image: Von Perry]
A solution for the labor crisis—and a new generation’s needs
Von Perry’s founders believe cities like Dallas should be open to the promise of concrete 3D printing as one way to address the growing labor crisis.
“Nobody wants to work with their hands anymore,” Joseph said. “They’re not interested in blue-collar labor. They want to work in the IT sector or some office job. Construction is a very hard, labor-intensive process and we have a labor shortage in the industry.”
Perry sees the appeal as generational.
“I’ve talked with a lot of young people who are about to buy homes and build homes,” Perry said. “One thing I’ve heard a lot is they want a home that looks like it was built in 2022. They want a fresh design, an open design. You really can’t get that from a lot of conventional construction methods.”
The founders say their clients—young or otherwise—can get it all in one place from Von Perry: an innovative architectural home design, a revolutionary 3D printing process, and the structural and construction work needed to finish the home.
Get on the list.
Dallas Innovates, every day.
Sign up to keep your eye on what’s new and next in Dallas-Fort Worth, every day.