If robots are taking over, MμZ Motion is poised to provide some of their mechanical guts with its patented motion systems.
But, there’s nothing to fear about the robotic future according to Carl Copeland, the founder and CEO of MµZ Motion.
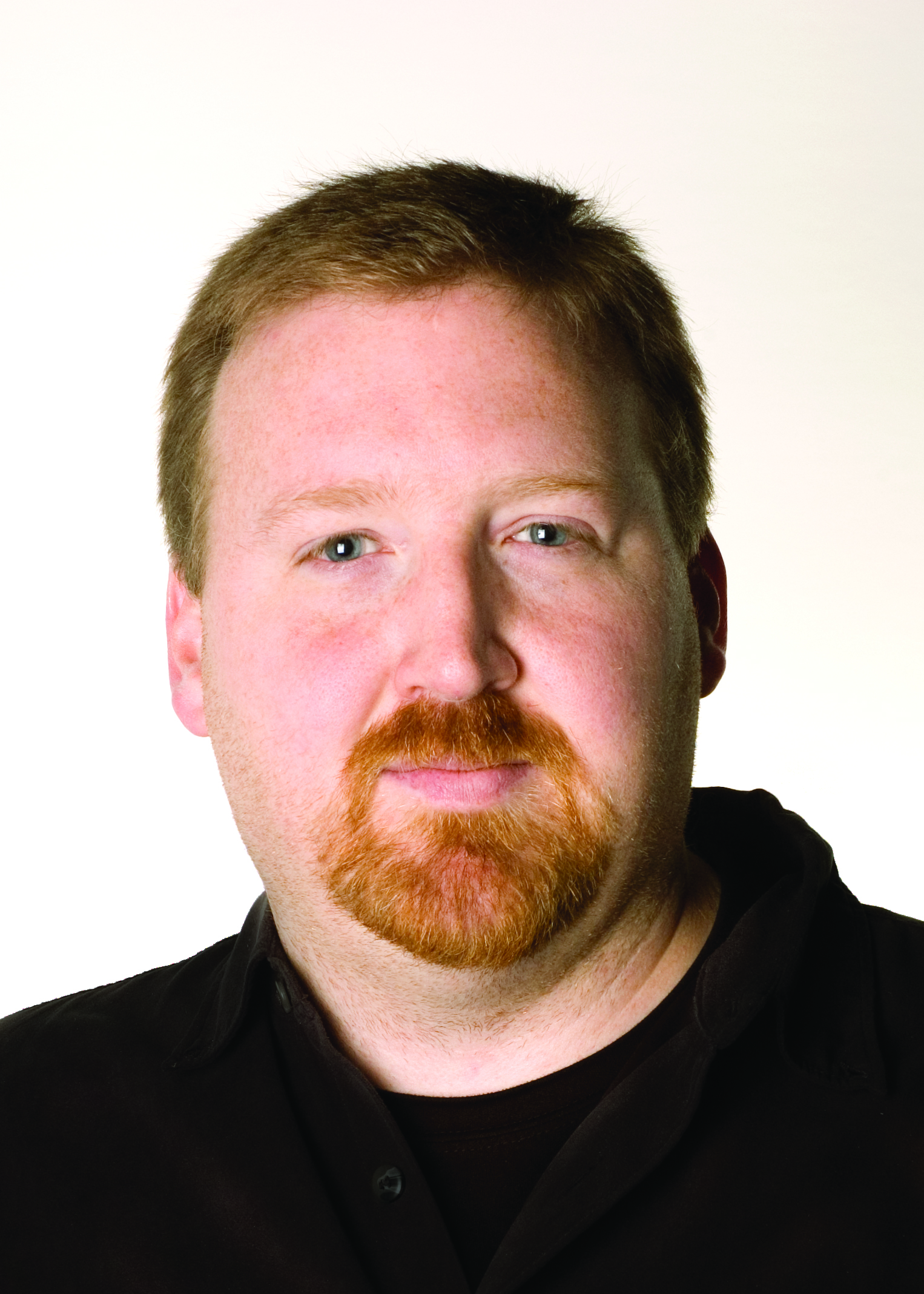
Carl Copeland
“You shouldn’t fall victim to the outcries of fear over humans being displaced, or worse, ruled by AI-empowered robot armies,” he says. “Robots and AI are just clever tools that increase productivity, quality of output, and quality of life.”
Automation is coming to many jobs as numerous studies and consultancy think tank white papers will attest, and innovation in collaborative robotics is part of what is making that possible. MμZ Motion is on the leading edge of the collaborative robotics—also known as COBOTS—space.
Along with Copeland, the Richland Hills-based startup is led by George Bennett, CTO, and Philip Lucia, CDO, as well as group of advisors with experience in motors and motion control, growing innovative tech companies, finance, and engineering.
MμZ Motion is early-stage, having secured $300,000 in friends and family investment as well as a seed commitment of $500,000 from a small group of investors expected to close by the end of this quarter. The goal is to raise between $1.5 million and $3 million to get into initial markets and reach positive cash flow, Copeland says.
Dallas Innovates caught up with Copeland for a Q&A on a range of topics including collaborative robotics, where the company is heading, and the story behind its interesting name.
Tell me about MµZ Motion.
MμZ Motion is a motion and control company that produces custom, high-performance motion systems (electric motors combined with electronic controls and geared drives) for the burgeoning robotics market, with a primary focus on the COBOT [collaborative robotics] and the AUTOMATA [humanoid robotics] markets.
Our patented Field Modulation Motion System [FMMS] is built on a hybrid servo motor that demonstrates performance features addressing the current limitations of contemporary robotics motion solutions.
The primary limitation affecting robotics is torque, or the force a motor can apply to a given application. Most motors are low-torque, so engineers are required to exchange the speed of a motor for the needed torque. This is done using a set of gears called a drive. There are high-torque motors, but they are so large and heavy that they aren’t feasible for robotics. Furthermore, they are constant-speed motors that take a lot of time to spin up and stop.
To deal with this problem, most of the robots you see in the media are powered by hydraulic motors. Hydraulics can deliver a fair amount of torque, but the cost is very poor “performance,” meaning the motors can’t really change directions quickly, and they have no inherent feedback system, so they are dangerous. If you get in the way of one of these robots, they go over you or through you. Developers have created systems that now produce amazing performances using hydraulics, complex sensors, and rapid actuators that control hydraulic valves to produce the current levels of performances, but they are still far away from the safe, reliable systems required for practical use.
The as-to-yet unreachable “flux capacitor” for robotics has always been a small, light electric servo motor with extremely high torque. A servo is a motor defined by its high performance. This performance is speed, or more accurately, quickness. The quicker a motor can accelerate and decelerate, the higher the performance. Servos are specifically designed to do this very quickly and accurately, but at the cost of torque. As a result, servos must rely on geared drives to convert their speed to torque. This trade then negates the quickness of the servo, while still delivering very low torque.
What differentiates the FMMS from current offerings is the unique and novel magnetics of our system. Our motor is more closely related to a transformer than an electric motor. Our magnetics allow us to deliver more than 10x the torque of a same-class servo while also performing at more than 30 times the quickness. The FMMS is an important advancement in robotics motion, expanding the application capabilities and market opportunities for the robotics industry.
In addition to the mechanical performances, our system reduces the magnetic materials by 80-85 percent and replaces the fixed structure with light weight polymers, ceramics and metamaterials. This enables us to deliver this “SciFi” ultra-light, high-torque servo that developers have been hoping for. Our motor, when comparing the torque delivered with other servos, is only 5 percent the weight per unit (Nm) of torque delivered.
I invented the new magnetics over 25 years ago. I spent years in my garage tinkering, testing, and improving the platform in the evenings and on weekends. Two years ago, I realized I had made a significant advancement in motion and started work on a production-ready design. What I ended up with was the first “paper” servo (it’s 85 percent cellulose fiber). From there I launched MµZ Motion in January 2018 with the backing of friends and family.
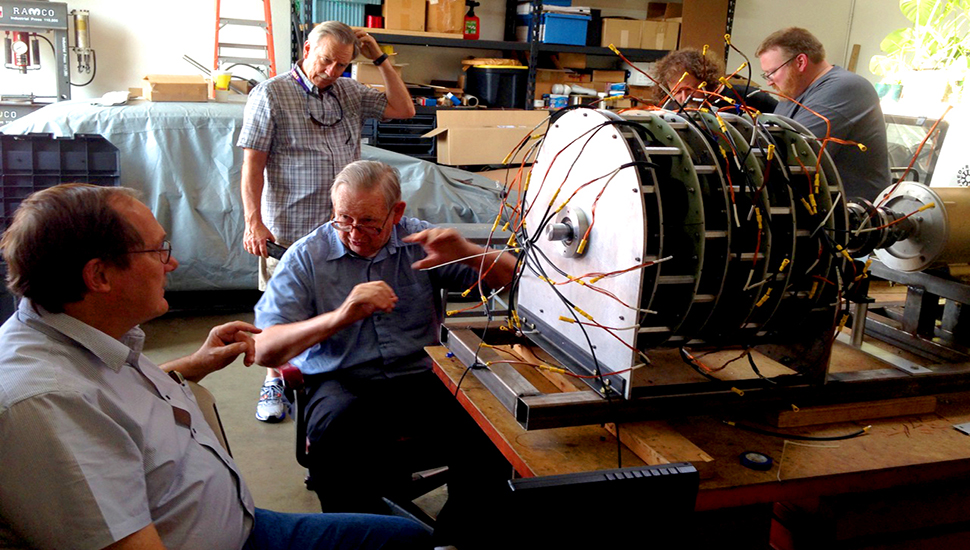
The MμZ Motion team works on a 24 inch servo. [Image: courtesy MμZ Motion]
Is there a story behind the company name?
MµZ is a multi-level play on words/terms/symbols.
The Greek symbol, µ, spelled out in English is “Mu” and pronounced myoo.
While in mathematics or metrics it’s used as the symbol for ‘micro’, in magnetic engineering it is the variable representing magnetic permeability (simply called ‘permeability’) in design equations.
Our motor uses a novel magnetic design that uses the effects produced by changes in permeability in a magnetic system. Normally, the permeability in a motor is a set quantity, but our system varies its permeability to increase magnetic affect and reduce traditional losses, so the µ is a critical variable.
Also, robots tend to be the muse of engineers, and the musings of a robotic future are part of the inspiration for most aspiring engineers.
So, the name references the symbol µ. Appealing to engineers, it references our system’s unique magnetics, and references our passion for our muse, robotics.
Our logo is also multi-layered. It’s constructed of 2 “M”s mirrored vertically, for MµZ Motion. In fact, a capital “M” is the capital form of Mu, “µ” being lowercase. It’s a stylized lemniscate/infinity (∞), idealizing our nearly unlimited application in motion. It’s also stylized to represent a butterfly, as I see our innovation as a transformative and emergent technology.
I overthink a great many things.
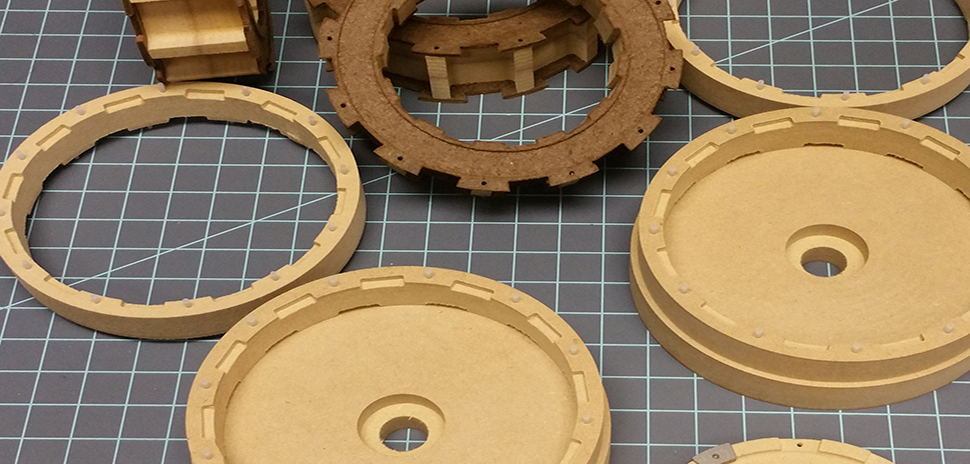
The MμZ Motion paper servo is made up of lightweight parts. [Image: courtesy MμZ Motion]
Explain the collaborative robotics market. How does it fit into robotics overall, and what are the main applications for products and services within the space?
Collaborative robotics, COBOTS, and the technology and performance features they employ, are the future of robotics, both industrial/commercial and personal. A COBOT is a specialized robot specifically designed for operation in human-occupied environments.
Conventional robots are unsafe for operation in human-occupied environments. They primarily use conventional hydraulic motors that are rudimentary machines. They have good torque, so they are used in large industrial robots, but these motors have no feedback system. If you get in the robot’s way, it goes through you or over you. Modern robots do have other sensor and safety systems, but if something unexpected happens, the motor simply cannot respond or stop fast enough.
COBOTS, by contrast, use a very high-performance motor called a servo. These motors are very quick and precise. They are able to move with accuracy measured in a few micrometers and can move from one position to another in the blink of an eye. Additionally, servos have position, speed, and force feedback. This enables a COBOT to sense when something unexpected has blocked its path. The system can measure the unexpected force and respond quickly enough that the robot can prevent injury or damage. These features produce robots that are safe for human augmentation and interaction. They are also capable of performing tasks that require a high degree of accuracy and force control.
In order for robots to interact with us in our daily lives, they must be able to respond and adapt to dynamic tasks and changing variables. They must also be able to ensure the safety of the people and objects around them. COBOTS embody all of these attributes.
Another unique feature of COBOTS is their ability to learn new tasks by manual input from an operator. This means you don’t need to be an engineer or programmer to setup and operate a COBOT. The same system that provides the safety feedback is the system used to program it.
Markets&Markets projected a CAGR of 57 percent for the U.S. COBOT market through the next five to seven years. If this prediction holds, the U.S. COBOT market would reach nearly $27 billion by 2027.
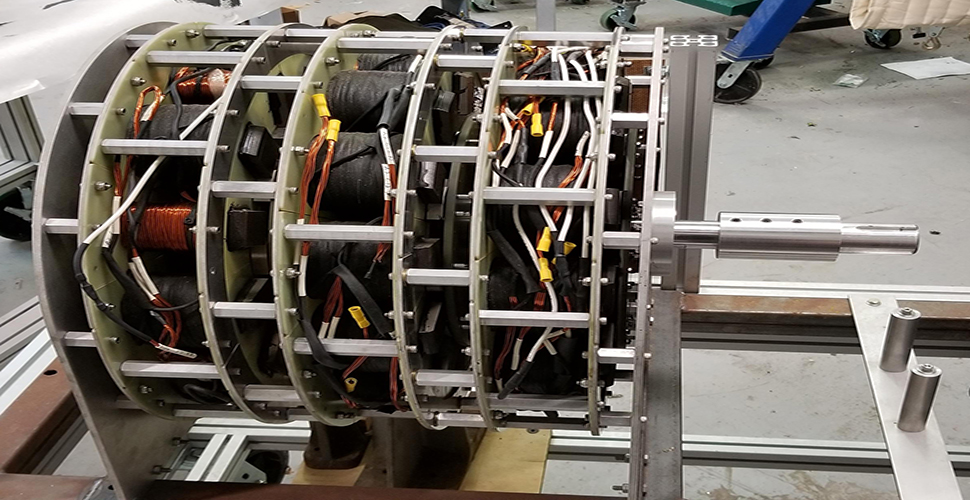
Pictured: a 24 inch servo. [Image: courtesy MμZ Motion]
What are some of the innovative products and technology that MµZ has created?
MµZ offerings are based on our novel Field Modulation Motor (FMM). This motor, and the specialized electronic controls that power it, present some very unique advantages over current systems.
The motor has a dual-stator configuration with an ultra-light rotor. This simply means that the prime components don’t move, so much less energy is spent in moving them as compared to other motors. The design also fragments the magnetics into several isolated, closed circuits. This allows for the greater magnetic effect with less steel and magnets, comparatively.
The fragmentation also enables us to scale the motor from diameters of less than 1/16 of an inch to greater than 50 inches. This means we can power both micro-scale robots and 30 to 40-foot robots.
Since we are able to substitute up to 85 percent of the motor’s mass with unconventional materials, this opens up a world of options and manufacturing processes. Applied correctly, we can reduce weight, increase tolerance to harsh environments (such as space/moon/ Mars/deep sea), and utilize the latest in additive manufacturing techniques and metamaterials.
Our design also provides a great deal of safety. Our motor can survive failures in up to 65 percent of its magnetics. Very few motors can survive more than one, if that. This is very important in robotics, because if a motor fails, the whole system can come crashing down, a very dangerous event if you are standing nearby. It’s even more important in an aerospace application. Redundancy is key to survivability, and our system provides several layers of it right out of the box.
Our control system is also very innovative. When configured accordingly, we can operate our motors’ multiple performance modes simultaneously. We can also switch between performances on-the-fly. We can even reconfigure the motor itself, with the controls, without physically altering the motor. Our system will open applications and markets that no one is currently considering servo motors for. Furthermore, our control advancements have application features translatable to conventional motors, meaning we can offer some of our performance-broadening features to existing designs.
We have also designed a rapid prototyping and low-rate production system, utilizing the additive and automated manufacturing options available to us that, when completed, will allow us to design, produce, and deliver custom systems in a fraction of the time it takes now.
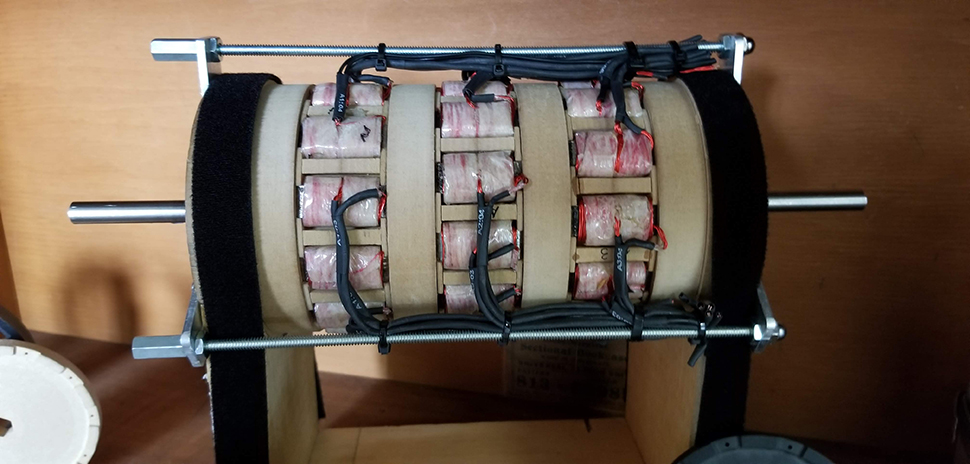
A MμZ Motion paper on display. [Image: courtesy MμZ Motion]
How important is innovation and staying ahead of the marketplace to the company?
We have a vastly superior motor that gives us a strong market advantage; however, we recognize the world waits for no one. Being a small startup, our speed to market, speed to adapt to customer/market demands, and speed to stay ahead of imitators and international patent infringement makes pacing ahead of the marketplace vital to our success.
This need is the reason we focused on additive and alternative manufacturing methods when designing the motor. In business it’s not, “the big eat the small,” it’s “the fast eat the slow.” We know that we will have to be fast and nimble in order to respond to market demand and contend with challenges from larger, more established competitors.
Our ability to rapidly innovate, and rapidly enter production with those innovations, is a big piece of our market strategy.
What are some interesting things about the robotics space overall that our readers might not know about, or might find surprising?
In my conversations, the most surprising fact for most is that the majority of robots (that aren’t toys) are hydraulically powered. Hollywood has set the expectation that robots are electric. While most of the systems are, electric motors with the torque to operate a robot larger than 12 to 18 inches are too heavy to be useable. They are almost entirely comprised of metal; steel, copper, and metal-ceramic magnets.
Imagine having a conventional motor in your wrist, elbow, and shoulder. In a robot, each joint needs at least two motors. Now extend the arm. The “arm” would be so heavy the “shoulder” could barely hold itself up, let alone perform any useful tasks. This is the dilemma motor developers constantly face.
Currently, hydraulic systems are the only practical option for them. The amazing robots Boston Dynamics is producing, for example, are hydraulic, even Spot, the dancing dog. An electric motor drives a hydraulic pump. Electric actuators open and close hydraulic valves to spin the hydraulic motors in different directions, and a vast network of sensors reads the motions, balance, forces, etc. to rapidly compensate in order to perform the stunts shown in their videos. What they have accomplished is amazing, but it’s even more so when you understand what challenges they are overcoming in the process.
Another item for thought is, what is a robot? A robot is any machine that performs pre-programmed tasks. Most don’t realize that almost all modern aircraft, trains, and commercial ships are robots. In a plane, for example, a human operator inputs commands through the flight controls, but the flight system is controlled by a computer that interprets these inputs and applies the needed movements and adjustments to the control surfaces and engines to affect the results the pilot is looking for. They have very sophisticated sensors and data analytics that compensate for the thousands of atmospheric and physical variables, shifts in load as passengers walk about, and even changes is air density as the aircraft ascends, descends, and experiences temperature and humidity fluctuations.
Locomotives are another robotic system. It’s almost entirely controlled from a few central stations. Locomotive engineers are mostly observers who provide intelligent, critical human oversight, but the system is almost completely autonomous.
The agriculture industry is another greatly automated robotic systems. One farmer can oversee 4-6 large harvesters or cultivators at once. Agriculture is responsible for most all the autonomous vehicle innovations that will drive our future autonomous cars.
We would already have our “George Jetson” robotic house servants if we had motors capable of powering them without complex, fragile, and inefficient gearing. Obviously, we are confident our system delivers these missing performances, but we’ve had a high enough level of electronics and AI to produce a useful humanoid, or AUTOMATA robot for years. The holdup is current motion systems.
While energy storage systems are another critical component for robotics, it’s not as critical for domestic robots as you might think. Nicola Tesla wirelessly powered most of his lab back in the very early 1900s. It really isn’t any more complicated to do it now. We should see early in-home service robots in the next 10-15 years.
What are the near- and medium-term plans for the company? Are there more products in development, either in the same market or maybe expanding your tech into new markets?
We are currently working to commercialize the production-ready system. We will be engaging our AUTOMATA partners by the end of Q2 with completed funding and have targeted the end of Q4 for our initial engagement of the COBOTS market.
We are simultaneously developing systems that will target aerospace, aeronautics, and biomedical. We can easily replace the hydraulic and pneumatic actuators currently used in aircraft. The size, weight, and redundancy of our motor makes it an obvious market. These markets, however, pose a regulatory barrier to entry that makes it a second-stage market.
A passion of mine is powered prostheses and exoskeletons. While most think of exoskeletons as a military application (or Ironman), it’s more realistic and beneficial application is providing or restoring quality of life to those who are disabled or physically limited. A dream of mine is to collaborate with Prof. Hugh Herr who heads MIT’s Biomechatronics Group. I’m not quite ready for him, but I will be soon. The idea of giving patients an intelligent, AI empowered, cybernetic limb that could deliver Olympic-athlete performances is exciting. I want to be clear, we aren’t building the devices, others are doing a tremendous job at that, right now. We are simply going to empower their devices with ours, making them ever more capable and impactful.
I expect that our tech will inevitably power most things that move. I have less-intelligent designs on the board that would provide all of our weight, size, and torque advantages to applications that don’t need servo-level performances. These motors would deliver an even greater amount of torque, as we no longer would need to preserve the speed performances. They would be perfect for all forms of transport and most heavy manufacturing applications.
I also have designs on my draft board that will offer a viable, efficient electric turbine for aerospace applications, but I think I’ll have to sit on that one for a while longer. Robotics is my focus for the foreseeable future.
Is there anything I haven’t asked about MµZ or your overall business space that Dallas Innovates’ readers should know?
You shouldn’t fall victim to the outcries of fear over humans being displaced, or worse, ruled by AI-empowered robot armies. Robots and AI are just clever tools that increase productivity, quality of output and quality of life.
The jobs they will be performing will relieve the humans currently performing those tasks, but they will simultaneously create a whole new class of jobs that make much better use of our ingenuity, creativity, and critical thinking, things only humans can do.
We humans can master and optimize tasks and operations at a lighting pace. COBOTS are just better ways to repeat and output those skills. I worked farms and ranches growing up. We were poor—very poor. I worked with people who didn’t even have a grade school education. In fact, I was the first male in my own family to complete high school. My point is that those whom I worked with were some of the most intelligent, resilient, creative, and masterful people I ever worked with. The problems they could solve, jigs they engineered, and skills they developed seemingly overnight always amazed and challenged me.
COBOTS will open job markets for those who might have been physically limited from participating in that field before. COBOTS will allow the skilled workers I just mentioned the ability to program their skill and capability directly into the robot through physical input.
They will take us out of roles that are hazardous, insufferable, or degrading to our minds and bodies through repetition. Humans are the most productive force on Earth, and that’s not changing anytime soon. A COBOT future is a hopeful and exciting future.
Get on the list.
Dallas Innovates, every day.
Sign up to keep your eye on what’s new and next in Dallas-Fort Worth, every day.