Roger Raley leads a team of engineers developing HX5: a lighter, faster-to-produce alternative to aluminum for aviation, defense, space, and more.
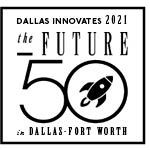
INVENTION
Load Lightener
Roger Raley
Less weight means less fuel, says Raley, president of Alpine Advanced Materials.
“Every gram of weight you save translates to less fuel you have to pay for and more distance you can travel, which we enable by making parts and components lighter,” he says. “With HX5, we can make traditionally aluminum parts and components at half the weight, and those parts can be engineered more easily and precisely.”
That’s key to making space flight more possible and more affordable. It also has implications for the pressing issue of carbon emissions in aerospace and defense.
Holding the exclusive global license to HX5, which was designed by Lockheed Martin Skunk Works, Alpine works with its clients to design and manufacture stronger and lighter components. The material represents more than a decade of testing and validation with an R&D investment of over $50 million.
In 2020, Raley’s team tested its patented flagship material in space, underwater, the desert, and extreme temperatures. It’s extremely versatile, he told Dallas Innovates. The company also sees broad applications for HX5, including marine and industrial parts, firearms, and bicycles.
Alpine has made a name for itself in commercializing high-performance materials originally developed and qualified by defense contractors to withstand conditions in extreme environments from the energy sector to aerospace. The components are used in jet fighters, high-speed helicopters, unmanned aerial vehicles, amphibious transport vehicles, rockets, satellites, and more.
Raley, who was a finalist in the D CEO and Dallas Innovates 2021 Innovation Awards in the transportation category, keeps an eye on the future. “The technological advances that we’re going to see in the next 20 years are almost unfathomable,” the innovator says in D CEO. “We’re going to see flying cars, we’re going to see commercialized space flight, and we’re going to see advances in medicine that will allow people to live significantly longer.”
But, he notes, “probably the most exciting is that, it’s not a matter of if, but when, we find life, in some form, in space. When it’s finally launched, the James Webb Space Telescope is going to discover some amazing things.”
What’s next? In response to the devastating impact of COVID-19 on travel, the company looks to partner with commercial airlines to help lower their costs for future air travel. in 2021, Raley expects to expand Alpine’s materials portfolio and increase the number of applications for parts made with HX5.
Meet the Innovator
Roger Raley was featured in Dallas Innovates’ Future 50 in Dallas-Fort Worth in the 2021 edition of our annual magazine. We talked with Raley, who joined the fast-growing company last summer, about the impact of an aluminum alternative, Alpine’s response to the pandemic, and how he encourages innovation in the team. Here’s our takeaway:
On HX5, Alpine Advanced Materials “game-changing” aluminum alternative:
Our most notable development has been expanding our understanding of exactly how much our flagship HX5 material can do. This year, we’ve tested its capabilities across a wide range of extreme environments—space, underwater, desert, air, extreme cold, and heat, among others—and we’ve proven just how extremely versatile it is. In doing this, we’ve also helped our clients improve the performance of their equipment, so they can make parts lighter, faster, and stronger.
Next year, we’re looking forward to continuing to push the business forward, growing these opportunities with our clients even in a challenging business environment, which is extreme in its own right.
On Alpine’s response to COVID-19:
We navigated COVID-19 by being ready, adaptable, and flexible, which is intrinsic to the culture we foster. Our focus lies in being both innovative and disruptive for our clients, which requires us to maintain an agile and responsive working environment. We reacted quickly to the direction of authorities and listened to the needs of employees. And because we had tools in place, we were able to adjust to remote work from day one. This summer, we also moved to a bigger office space in South Side on Lamar that meant employees could return to a safer and more socially distant workplace.
On teamwork in difficult times:
We have always encouraged employees to feel empowered to make decisions without being afraid to take risks—our clients taken risks by changing how they engineer parts, so we too need to walk that walk. In challenging established industries to change decades-old methods, our employees had already developed a resilience that served them as we faced these difficult times together. Throughout lockdown, we maintained open communication, checking with each other every day because we first and foremost valued making sure our employees were okay. It also helped to show them how resilient we as a company were as we defied the odds by growing our business and our team this year.
The Q&A was edited for brevity and clarity. A version of this story was originally published in Dallas Innovates 2021: The Resilience Issue.
Read it online
Our fourth annual magazine, Dallas Innovates 2021: The Resilience Issue, highlights Dallas-Fort Worth as a hub for innovation. The collective strength of the innovation ecosystem and intellectual capital in Dallas-Fort Worth is a force to be reckoned with.
Get on the list.
Dallas Innovates, every day.
Sign up to keep your eye on what’s new and next in Dallas-Fort Worth, every day.